Vacuum Pumps: Essential Components in Milk Machinery

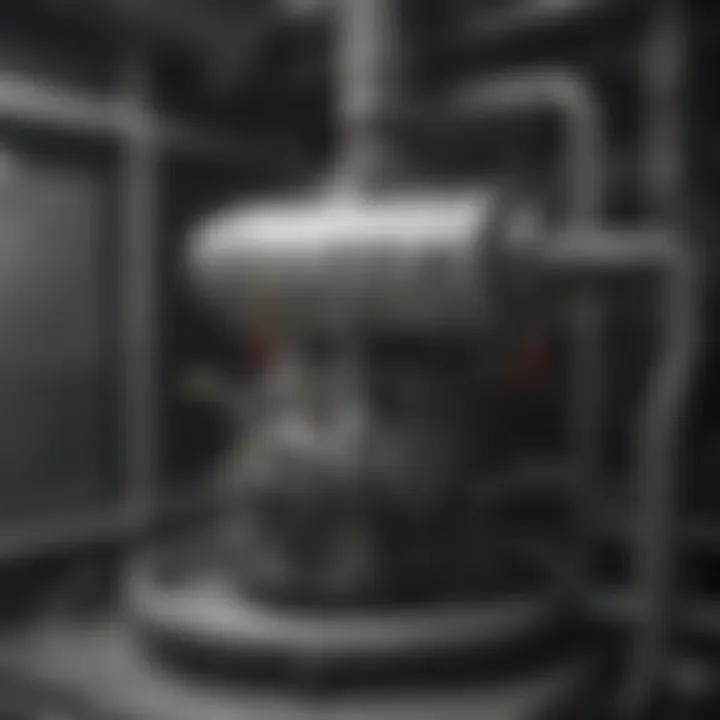
Intro
In the fast-evolving landscape of dairy production, vacuum pumps play a pivotal role. These devices are not just mechanical tools; they are the heartbeat of milk machinery, influencing the efficiency and quality of milk extraction. Understanding their function and significance is foundational for anyone involved in dairy farming—be it a seasoned farmer or a newcomer eager to learn.
In this article, we will explore the intricate relationship between vacuum pumps and milk machinery, dissecting how these pumps operate, their specifications, and how proper maintenance extends their lifecycle. Furthermore, we'll analyze their impact on milk quality and how they contribute to the overall productivity of dairy farms.
Current Trends in Agriculture and Horticulture
The agricultural sector is currently witnessing a wave of innovations aimed at enhancing productivity while minimizing environmental footprints. These trends are not just passing fads but represent a shift in how farming—especially dairy farming—is perceived and implemented.
Overview of Recent Innovations
Modern vacuum pump technology has seen improvements in efficiency and reliability. Manufacturers are integrating digital interfaces and smart technology, allowing farmers to monitor pump performance from their smartphones.
- Energy-Efficient Designs: Recent models consume significantly less energy, helping to reduce operational costs.
- Automated Systems: Automation allows for precise control in the milking process, enhancing both output and milk quality.
- Real-Time Monitoring: Some pumps now feature sensors that send alerts if there’s a drop in performance, enabling immediate maintenance.
Sustainable Practices Gaining Popularity
As concerns regarding sustainability grow, dairy farmers are increasingly seeking eco-friendly solutions. Vacuum pumps are not exempt from this trend.
- Recycling Technologies: Some systems include mechanisms to treat and reuse water used in the milking process, reducing waste.
- Reduced Emissions Systems: New designs focus on minimizing air emissions, contributing to a cleaner environment.
Essential Farming Techniques
Equipped with advanced tools, farmers improve their practices and outcomes. Essential farming techniques revolve around intertwining good practices with technology.
Soil Health Management
Healthy soil is crucial for sustainable farming. Good soil quality leads to healthier cows, which in turn produce better milk. Strategies such as crop rotation and cover cropping help maintain soil integrity.
- Cover Cropping: Planting cover crops in off-seasons enriches the soil.
- Organic Amendments: Using natural fertilizers like compost boosts microbial activity.
Pest and Disease Control Strategies
Controlling pests and diseases is vital for maintaining healthy livestock. Integrated Pest Management, or IPM, combines various techniques for effective pest control.
- Biological Control: Utilizing natural predators to manage pest populations.
- Crop Diversity: Growing a diverse range of plants can disrupt pest life cycles and improve resilience.
Tools and Technology in Farming
The right tools can make all the difference on a farm. Technology is becoming ingrained in day-to-day operations, reshaping the future of dairy farming.
Overview of Advanced Farming Tools
Beyond vacuum pumps, several cutting-edge tools are revolutionizing dairy farming. Sensors, drones, and data analytics are just a few examples.
- Drones for Monitoring: Drones provide aerial views, aiding in crop health assessments.
- Data Analytics: Farmers use software solutions to analyze performance metrics, helping to inform better decisions.
Case Studies on the Use of Technology
Two contrasting examples illustrate how technology can enhance dairy operations.
- Case Study 1: A farm in Wisconsin adopted automated milking systems integrated with AI-driven data analysis tools, resulting in a notable increase in milk yield.
- Case Study 2: A small-scale farm in Vermont implemented sustainable practices alongside traditional techniques, ensuring consistent quality in milk while maintaining environmental stewardship.
"Investing in the right technology isn't just about efficiency; it's about securing a sustainable future for farming."
The intersection of innovation, sustainable practices, and robust farming techniques positions vacuum pumps as a crucial element in dairy production today. As we continue, we will delve deeper into how these pumps operate, their specifications, and the best practices for maintenance that every dairy farmer should know.
Prolusion to Vacuum Pumps in Dairy Operations
In the bustling world of dairy farming, vacuum pumps are the unsung heroes behind the curtains. They play a vital role in the efficient operation of milk machines. Without them, the entire milking process would be akin to trying to breathe underwater; nearly impossible and certainly messy. This section will offer a deeper understanding of how vacuum pumps function and why they are indispensable in modern dairy operations.
Overview of Dairy Production Processes
Dairy production involves several intricate processes that ensure not just quantity but quality of milk. From milking to pasteurization, each step is designed to uphold the standards of safety and taste. The milking process itself can be physically demanding for both the animals and the equipment. Here, vacuum pumps step in to streamline operations.
When a cow is milked, the objective is to mimic the natural sucking action of a calf. This is where vacuum technology plays its part, creating a controlled environment that promotes efficient and gentle milking. In a typical milking setup, vacuum pumps function by generating a pressure difference, allowing the milk to flow smoothly from the udder to storage tanks. This is all about ensuring that the cows are not stressed during the process, which, in turn, leads to higher quality milk production.
Importance of Vacuum in Milking Systems
The importance of vacuum in milking systems cannot be overstated. It serves multiple purposes:
- Efficiency: Vacuum systems drastically cut down the time taken for milking, allowing dairy farms to increase their output without compromising on quality.
- Animal Welfare: Cows experience less discomfort during milking when vacuum systems are finely tuned to mimic natural sucking. Happy cows produce better milk.
- Hygiene: Vacuum pumps help maintain a closed system which reduces exposure to contaminants, thus preserving milk quality.
- Flexibility: Different milking styles can be accommodated through adjustable vacuum levels and configurations, essential for various farm setups.
"A good milking system is as crucial to dairy farming as the feed that sustains the cows. Vacuum pumps make this system run smoothly and efficiently."
Types of Vacuum Pumps for Milk Machines
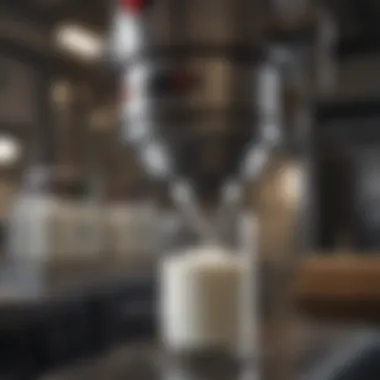
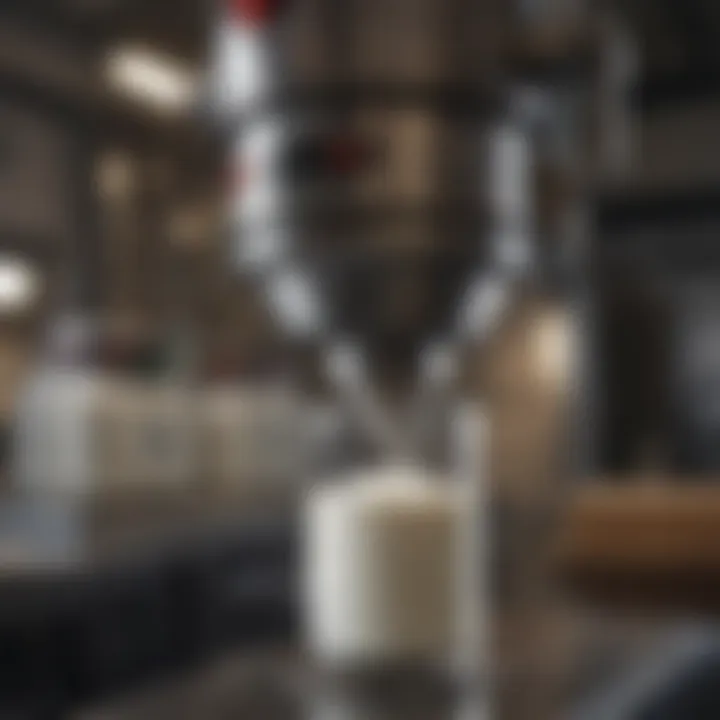
Understanding the types of vacuum pumps used in milk machines is crucial for dairy farmers and enthusiasts. The right pump can significantly affect milking efficiency, cow comfort, and ultimately, milk quality. With different designs tailored to specific applications, each type of pump brings its own set of advantages and operational considerations. Choosing the right vacuum pump can lead to enhanced productivity, and better dairy management.
Positive Displacement Pumps
Positive displacement pumps are a foundational element in many milking systems. They function by trapping a fixed amount of liquid and then forcing that volume into the discharge pipe. This design is particularly beneficial in creating consistent flow rates and maintaining stable vacuum levels, which is essential for reliable milking.
One of the key benefits of positive displacement pumps is their capacity to handle varying liquid viscosities. In practical terms, this means they can efficiently pump not only milk but also other dairy by-products without losing efficiency. Moreover, these pumps tend to be more effective at lower speeds, making them energy-efficient and cost-effective over time.
However, they do have some downsides. If not maintained properly, wear and tear can result in increased leakage, leading to a drop in efficiency. The initial setup costs might be higher than that of dynamic pumps, but this is often balanced out by their durability and lower operational expenses.
Dynamic Pumps
Dynamic pumps operate quite differently from their positive displacement counterparts. Instead of using a fixed volume mechanism, they rely on the kinetic energy of a rotating impeller or similar component to create flow. This type of vacuum pump is particularly adept at generating higher flow rates, making them suitable for larger dairy operations where speed is crucial.
The advantages of dynamic pumps include their lightweight structure and ability to handle high volumes of land, thanks to their continuous operation. Farms focusing on efficiency often prefer these pumps for their speed and their capability to produce a strong vacuum quickly.
However, dynamic pumps are not without their drawbacks. Maintaining a constant vacuum level can be challenging, especially if the system experiences fluctuations in flow demand. Additionally, they may require more frequent maintenance to ensure optimal performance. As a result, while they can be ideal for some setups, farmers must weigh their specific needs carefully when considering this option.
Comparison of Pump Types
When deciding between positive displacement and dynamic pumps, it's essential to be familiar with the pros and cons of each:
- Positive Displacement Pumps
- Dynamic Pumps
- Pros: Consistent flow rates, efficient at lower speeds, can handle varying viscosities.
- Cons: Higher initial costs, potential for efficiency loss with wear and tear.
- Pros: High flow rates, lightweight and fast, suitable for larger operations.
- Cons: Difficulty in maintaining constant vacuum, may require more maintenance.
How Vacuum Pumps Operate
Understanding how vacuum pumps operate is fundamental in grasping their significance in dairy milk machines. These pumps are not merely mechanical devices—they are the beating heart of efficient milking operations. Knowing the inner workings helps farmers select the right equipment, troubleshoot issues, and ultimately enhance both productivity and milk quality.
Basic Operational Principles
At the core of vacuum pump functionality is a straightforward principle: they remove air from a designated space to create a vacuum. This vacuum is essential for drawing milk from the cow's udder without causing harm or discomfort. The process is typically initiated when the pump starts, resulting in a drop in pressure that allows milk to flow smoothly through the system. It’s a bit like drawing a drink through a straw; without creating that negative pressure, nothing flows.
Moreover, vacuum pumps can be classified based on their operational cycle:
- Continuous: These pumps run repeatedly to maintain consistent vacuum levels.
- Intermittent: They cycle on and off, allowing for pauses in operation which can be beneficial for certain dairy setups.
The choice between the two often hinges on the specific needs of the dairy operation, be it scale, type of livestock, or even the complexity of the milking setup.
Components of Vacuum Pumps
Every vacuum pump is comprised of several critical elements, each playing a significant role in its overall function:
- Motor: This is the powerhouse that drives the entire system, typically electric, ensuring efficient performance.
- Pump Chamber: Where the action happens; this chamber houses the mechanisms that create the vacuum.
- Inlet and Outlet Valves: These control the flow of air in and out of the pump chamber, ensuring that the vacuum is maintained effectively.
- Filters: Essential for maintaining air quality and preventing contaminants from entering the system, these components play a crucial role in sustaining milk hygiene.
Each component must be well-maintained; otherwise, the efficiency of the pump can drastically diminish, affecting the entire milking process.
Performance Metrics
Evaluating vacuum pumps isn't just about their mechanical features. Performance metrics help assess their effectiveness and overall value in a dairy operation. The following key factors are considered:
- Vacuum Level: Measured in inches of mercury (Hg) or millibars, the vacuum level directly impacts milk flow rates.
- Cubic Feet per Minute (CFM): Indicates the volume of air the pump can move and is pivotal for ensuring that the vacuum system can handle the turmoils of milking multiple cows efficiently.
- Noise Levels: A quieter pump not only improves the working environment but is also a reflection of quality engineering.
- Energy Efficiency: ESG (Environmental, Social, and Governance) concerns aside, less power consumption leads to lower costs, which is critical for the bottom line.
"When selecting a vacuum pump, understanding and prioritizing these performance metrics can lead to significant differences in operational outcomes."
In sum, knowing how vacuum pumps operate involves understanding the principles, components, and metrics that define their performance. Educating oneself on these facets ensures that farmers are not just mechanically savvy but also equipped to optimize their milking processes.
Selecting the Right Vacuum Pump for Milk Machines
Choosing the proper vacuum pump for milk machines is critical in maximizing efficiency and ensuring high milk quality in dairy operations. The right selection can make or break the profitability and effectiveness of milking systems. With various types of pumps available, each with distinct capabilities and applications, making an informed choice can lead to better performance and reduced operational costs.
Factors Influencing Selection
When it comes to selecting a vacuum pump, several factors play a significant role. These encompass:
- Farm Size and Scale: Larger dairy farms may require more robust pumps due to higher milking demands. Knowing your farm's scale helps identify the pump capacity needed.
- Type of Milking System: Different milking systems hold varying requirements. A pipeline system may need a different pump type than a bucket milker system.
- Energy Efficiency: Opting for pumps with better energy efficiency can lead to significant cost savings. Look for models that are designed for optimized performance without excessive energy consumption.
- Maintenance Requirements: Some pumps may necessitate frequent upkeep due to sensitive components. It's advisable to consider ease of maintenance to minimize downtime.
Each of these factors intertwines to guide optimal pump selection, making it essential to weigh them against individual farm conditions.
Evaluating Pump Specifications
Once you've outlined the essential factors, it's important to delve into the specific specifications of potential vacuum pumps. Key specifications to evaluate include:
- Flow Rate: The flow rate should align with your milking capacity. A pump with too low of a flow rate can lead to inefficiencies.
- Vacuum Level: Different milking processes require different vacuum levels. Understanding the vacuum needs based on the system design is crucial to select a pump that delivers it effectively.
- Noise Level: In concentrated operations, excessive noise could disturb both the animals and the workers. It's wise to scrutinize the noise output of potential pumps.
- Material and Durability: Opting for pumps made from robust materials ensures longevity and durability, especially in harsh farm environments.
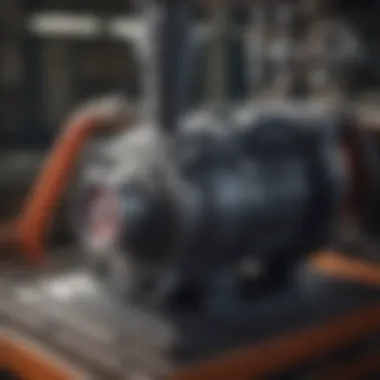
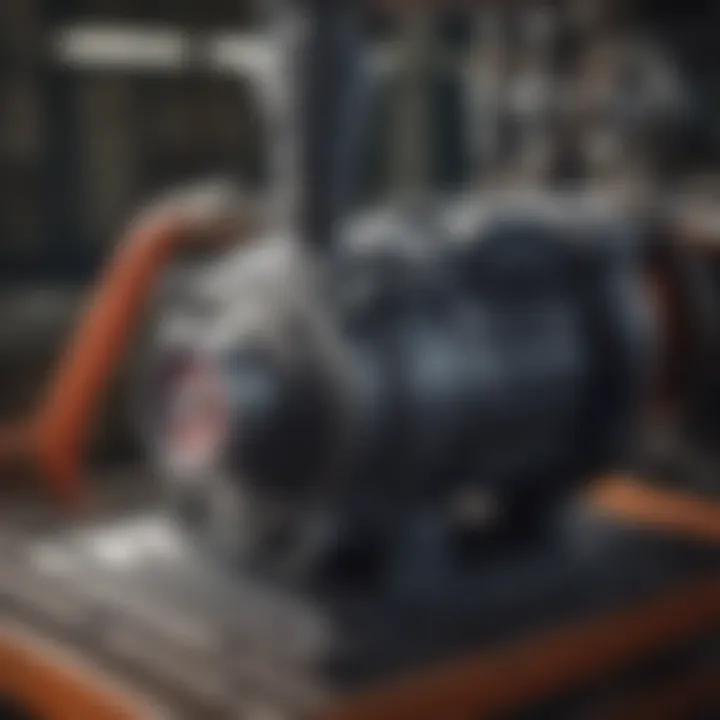
These specifications are crucial for evaluating the capacity of a vacuum pump to meet the precise needs of your dairy operation.
Brand Comparisons and Options
With a variety of brands on the market, understanding the pros and cons of different options can help streamline your purchasing decision. Notable brands in the vacuum pump industry include:
- DeLaval: This brand is known for its advanced technology and durable designs, catering primarily to large dairy operations.
- Boumatic: Offering a range of pumps specifically optimized for milk production, Boumatic emphasizes energy efficiency and user-friendly maintenance.
- MilkingSystem: Their focus on smart farming solutions integrates well with modern dairy practices, providing excellent automation features.
- GEA Farm Technologies: Renowned for its quality and innovative approaches, GEA pumps deliver reliability for various milking configurations.
"Investing in a reputable brand often leads to better performance on the farm."
Evaluating various brand reputations, consumer feedback, and longevity in the field can provide insights that clarify your selection process. Moreover, engaging with other dairy farmers, perhaps through platforms like reddit.com or dedicated agricultural forums, can yield real-world experiences that inform your choice.
In summation, selecting the right vacuum pump involves a thorough understanding of your specific needs, assessing pump performance based on specifications, and making informed comparisons among available brands. This careful deliberation ultimately serves as a backbone to achieving optimal results in dairy milk production.
Maintenance of Vacuum Pumps
Keeping vacuum pumps in optimal working condition is not just a best practice; it's essential for maintaining the efficacy of milk machines in dairy operations. Well-maintained pumps not only extend the lifespan of the equipment but also ensure that the quality of milk collected remains high. Neglecting maintenance can lead to costly repairs and downtime, which could impact productivity on the farm.
Routine Maintenance Practices
Regular maintenance practices go a long way in ensuring that vacuum pumps function efficiently. Here are key practices to consider:
- Filter Cleaning/Replacement: Dust and debris can accumulate in filters. Regular checks and cleaning or replacing them is vital to maintain airflow and vacuum pressure.
- Checking for Leaks: Small leaks can cause significant drops in pump efficiency. Regular inspections of hoses and connections help in spotting leaks early.
- Oil Checks: If the pump is oil-lubricated, keeping an eye on oil levels and quality is crucial. Contaminated oil can damage internal components, so it should be changed periodically.
- Belt and Pulley Inspectitons: Ensure the belts are not frayed and the pulleys are aligned. Misalignment can lead to excessive wear.
Following these practices boosts the reliability of the system and keeps operational disruptions at bay.
Common Issues and Troubleshooting
Despite regular maintenance, issues can still crop up. Here’s a list of common problems along with their possible solutions:
- Low Vacuum Pressure: This often signals a leak somewhere in the system. Check for any loose fittings or damaged hoses.
- Overheating: If the pump runs hot, it could be due to low lubricant levels. Check the oil levels, and if they’re fine, look at the airflow around the motor.
- Strange Noises: Any odd sounds can be a sign of internal wear or misalignment. Listening carefully while the machine operates can help in identifying such problems early.
If issues persist, considering the pump’s overall condition can help inform whether repairs or replacement are necessary.
When to Seek Professional Help
There are times when DIY trouble shooting just doesn’t cut it. It’s important to know when to call in a professional:
- Complex Mechanical Failures: If you notice internal failures like wearing gears or damaged seals, it’s better to seek expert help.
- Unabated Performance Issues: When routine checks and fixes do not solve persistent problems, it’s time to bring in a technician.
- Missing Specialized Knowledge: If there’s a technology upgrade or advanced system integration you’re not familiar with, a professional’s expertise can be invaluable.
Remember, sometimes it’s more cost-effective in the long run to bring in a professional than to tinker endlessly and risk further damage.
Routine attention to these factors will not only maintain the vacuum pumps but also enhance overall milk quality and operational efficiency on the dairy farm.
Impact of Vacuum Pumps on Milk Quality
The quality of milk is a pivotal aspect of dairy production. It's not just about quantity; it's about delivering a product that meets stringent safety and taste standards. Vacuum pumps play a fundamental role in ensuring that milk is collected efficiently while maintaining its integrity. Understanding the impact of these pumps on milk quality involves digging into their influence on physical characteristics, contamination levels, and overall consumer satisfaction.
Relationship Between Vacuum and Milk Integrity
The relationship between vacuum and milk integrity can’t be understated. When vacuum pumps are employed correctly, they create a consistent and stable environment that aids in the effective removal of milk from the udder. This stability is key in preventing any bruising or damage to the milk. If the vacuum level is too high, however, it can lead to excessive pressure that may cause harm to the teat and result in a decrease in milk flow. Similarly, insufficient vacuum levels can hinder the milking process, causing unrest in the cow and potentially leading to contamination of the milk.
Furthermore, an ideal vacuum pressure ensures that the milk is not exposed to unnecessary bacterial growth during the milking process. By effectively sealing the milking apparatus, vacuum pumps reduce the chances of outside particles entering the system, thus preserving the milk's quality as it is extracted.
Effects on Bacterial Counts
Bacterial counts in milk are a major concern for dairy producers, as they directly affect product quality and compliance with health regulations. Vacuum pumps contribute to maintaining lower bacterial counts by minimizing the exposure of milk to the external environment. When milking machines are properly maintained, the vacuum system can effectively prevent the backflow of milk, which can introduce bacteria into the milk.
- Proper adjustments of vacuum levels help in:
- Ensuring quicker milking times, reducing the time milk spends in contact with the air, thus lowering contamination risks.
- Creating an environment where milk travels through sanitized tubing directly to storage.
This diminished exposure leads to healthier milk with bacterial populations within acceptable limits. Regularly monitoring vacuum pumps ensures that they perform optimally without manual interference, thus promoting the overall hygiene of the dairy operation.
Sensory Attributes of Milk
The sensory attributes of milk, such as taste, aroma, and texture, are critically influenced by the conditions during the milking process. Vacuum pumps indirectly affect these attributes through their role in managing how efficiently milk is collected. For instance, if milk is subjected to high temperatures or prolonged exposure to air due to poor vacuum levels, it can develop off-flavors and undesirable aromas.
An optimum vacuum system:
- Maintains the freshness of milk by ensuring that it is extracted quickly and efficiently.
- Reduces agitation, which can alter the milk's texture and flavor profile.
Dairy farmers must keep an eye on these sensory qualities, as they can determine marketability. A consistent, high-quality product not only wins over customers but can also enhance a farmer's reputation.
"In the dairy business, the proof is in the pudding —or in this case, the milk. A good quality product is always the best advert for your operation."
In summary, vacuum pumps are more than just mechanical devices; they are pivotal in the quality assurance of milk. Understanding their impact allows dairy producers to optimize their systems and ensure the delivery of the best product to the consumer.
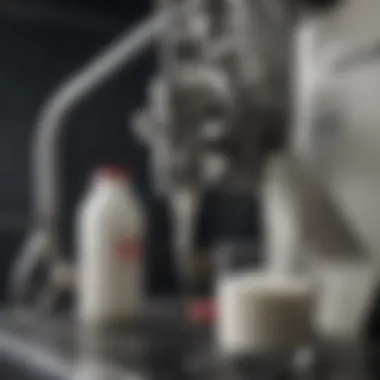
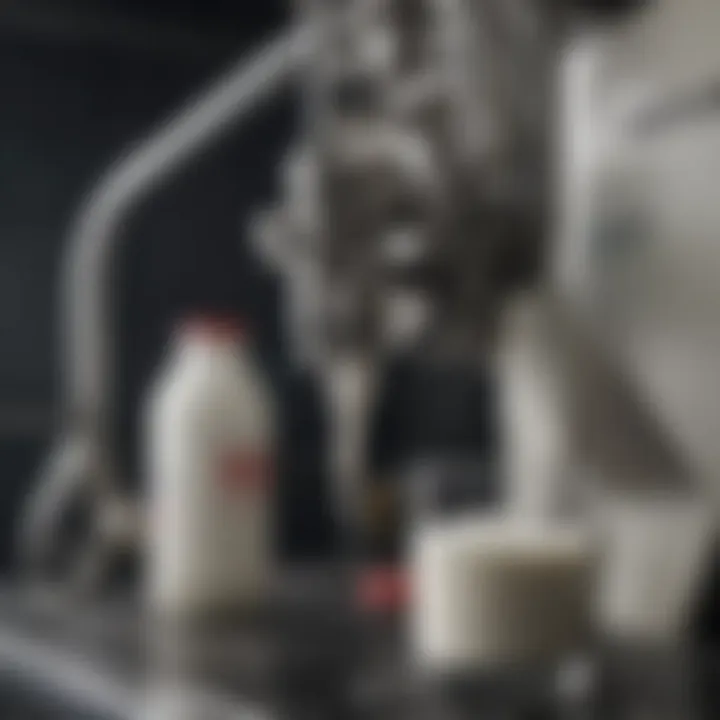
Economic Considerations in Vacuum Pump Use
In the world of dairy production, vacuum pumps are more than just mechanical components; they are pivotal to financial health and operational efficiency. Understanding the economic considerations surrounding their use is key for farmers looking to maximize both profits and productivity. Each dollar spent can translate to time saved, improved milk quality, or reduced operational hassles—all vital in keeping a farming operation afloat.
Investment vs. Return
When it comes to vacuum pumps, the initial investment can often seem hefty. However, it's essential to weigh this cost against the potential returns. For instance, investing in a high-quality vacuum pump can lead to significant benefits such as:
- Increased Efficiency: A reliable pump can ensure optimal milking times and reduce the frequency of downtime, which maximizes overall production.
- Lower Operating Costs: Energy-efficient pumps consume less power, helping to bring down utility bills over time.
- Higher Milk Quality: Quality equipment can contribute to higher standards in milk production, enabling producers to fetch better market prices.
The challenge, of course, lies in calculating the expected return on investment (ROI). Many farmers might overlook the long-term savings and benefits in favor of cheaper, less efficient options.
Cost-Benefit Analyses
Engaging in a cost-benefit analysis isn’t just a good idea; it’s practically mandatory when selecting a vacuum pump. This method allows farmers to critically assess all potential costs—including purchase, operation, maintenance, and possible repairs—against the anticipated benefits, both tangible and intangible.
Key points to consider in your analysis include:
- Maintenance Costs: Some pumps may seem cheaper at first glance but could require more frequent repairs. Factor that into your calculations.
- Pump Longevity: The lifespan of a pump affects its total cost. A more durable model may require a larger upfront investment but could lead to savings in the long run.
- Operational Flexibility: Pumps that can adapt to different milking systems could save you from additional expenses when upgrading other equipment.
"Choosing the right vacuum pump is a mix of art and science. Even if it costs a bit more upfront, you can gain much in efficiency and quality."
Long-term Efficiency Gains
Long-term efficiency is a buzzword in the agricultural sector. However, it deserves serious attention in the context of vacuum pumps. Efficient machines lead to better practices that can shape future success in milking processes. Here’s how:
- Consistent Performance: Quality vacuum pumps that operate efficiently tend to offer stable performance, reducing the variability in milk production.
- Workforce Productivity: With fewer mechanical issues, staff can focus more on milking and quality control rather than dealing with equipment failures.
- Reduced Waste: Efficient vacuum pumps minimize the chances of milk spills or contamination, both of which can significantly affect bottom lines by reducing yield.
When evaluating long-term efficiency, farms should look beyond simple costs and consider how improved technology can lead to sustainable practices and future profitability.
In sum, understanding the economics of vacuum pumps is a critical aspect not just of operating, but thriving in the dairy industry. With careful analysis and planning, investments in vacuum pumps can yield significant returns, enhancing not only the bottom line but also the quality of dairy products in the competitive market.
Advancements in Vacuum Pump Technology
The world of dairy farming is evolving, and with that evolution comes the need for more efficient, effective, and sustainable practices. Advancements in vacuum pump technology play a crucial role in this shift. As farms become larger and milk production increasingly automated, the demands on milking machinery grow. New technologies help meet these demands while ensuring quality and sustainability. The significance of these advancements extends beyond mere efficiency; they forge pathways toward a greener future in dairy operations.
Emerging Technologies in Dairy Pumps
In recent years, dairy pumps have seen revolutionary changes. For instance, the introduction of variable frequency drives (VFD) allows for pumps to operate at different speeds. This flexibility helps save energy—something every farmer is keen on, seeing as energy costs can eat up profits.
Another compelling development is the integration of smart sensors. These sensors continually monitor pressure, flow rates, and other key parameters, providing real-time feedback. Farmers can thus address potential issues before they escalate, ensuring that everything runs smoothly.
- Smart Sensors: Monitor pump performance in real-time.
- Energy-Efficient Motors: Reduce electricity consumption.
- Compliance Features: Ensure adherence to health standards.
The goal is to reduce downtime and increase productivity, which is particularly important during peak milking seasons.
Automation and Integration in Farming Systems
Automation is no longer a buzzword; it is a reality in dairy farms across the globe. Many new vacuum pump models integrate seamlessly with existing farm management systems. This integration facilitates a comprehensive view of dairy operations, allowing farmers to manage their resources efficiently.
Using software that connects to vacuum pumps, it's possible to schedule maintenance, track usage, and even monitor the health of dairy cows all in one place. This interconnected approach can lead to significant savings and boosts productivity.
For instance, a farmer can set up alerts for maintenance needs or performance dips directly on their mobile device. This means they don’t have to be physically present, offering them flexibility and peace of mind.
Sustainability Considerations
With public scrutiny on how agricultural practices impact the environment, sustainability has become a hot topic. Advanced vacuum pump technology contributes to these efforts. Energy savings play a significant role, as these modern systems often consume substantially less power compared to older models.
Moreover, the manufacturing processes for these pumps are becoming greener. Companies are increasingly using recyclable materials and reducing waste during production.
Here’s a brief overview of sustainability aspects in modern vacuum pump technology:
- Energy Efficiency: Lower power consumption leads to lower carbon footprints.
- Durability: Longer-lasting equipment means fewer replacements, which is better for landfill waste.
- Reduced Water Usage: Innovative designs often require less water for cleaning processes.
Maintaining a focus on sustainability not only resonates with consumers but also aids in compliance with increasingly stringent regulations. As the dairy industry strives to integrate greener practices, improved vacuum pump technology is at the forefront of this endeavor.
By investing in advanced vacuum pump technologies, dairy farmers are not just ensuring better efficiency but also paving the way for a sustainable future in dairy production.
Finale
The discussion on vacuum pumps in milk machines cannot be overstated. These devices don’t merely facilitate the extraction of milk; they play a pivotal role in ensuring efficiency, hygiene, and ultimately, the quality of the product. Understanding their significance equips dairy farmers and stakeholders with vital insights that can lead to improved operational practices.
Summary of Key Points
In summary, several crucial aspects emerge from our exploration of vacuum pumps:
- Functionality: Vacuum pumps create a consistent negative pressure, allowing milk to flow smoothly and efficiently from the udder to the storage tanks. This process is fundamental to modern dairy operations.
- Quality Control: By maintaining appropriate vacuum levels, these pumps help in reducing bacterial contamination and preserving milk integrity. Monitoring the vacuum levels can directly correlate with the quality of the milk produced.
- Maintenance Practices: Routine checks and timely troubleshooting of vacuum systems can prevent costly downtimes. Understanding common issues can save both time and resources.
- Technological Advancements: Continuous improvement in vacuum pump technology emphasizes sustainability and reduces operational costs. Automation in dairy farms is transforming traditional methods, enhancing productivity.
Future Outlook for Vacuum Pump Applications in Dairy
Looking ahead, the role of vacuum pumps is set to evolve even further. The dairy industry is on the brink of several transformations driven by emerging trends:
- Integration with Smart Technology: Farmers are increasingly adopting precision farming techniques. Incorporating smart vacuum pumps that can monitor and adjust parameters in real-time will likely become standard. This shift will enable better resource management and efficiency.
- Focus on Sustainability: As environmental standards intensify, the emphasis on eco-friendly vacuum systems will gain traction. Innovations aimed at reducing energy consumption can cut costs and minimize the carbon footprint of dairy production.
- Enhanced Data Analytics: Big data and analytics can provide deeper insights into system performance. This approach can lead to proactive maintenance predictions and improved troubleshooting strategies, thus optimizing milk production processes.