Understanding 3 32 Aircraft Cable: Specs & Uses
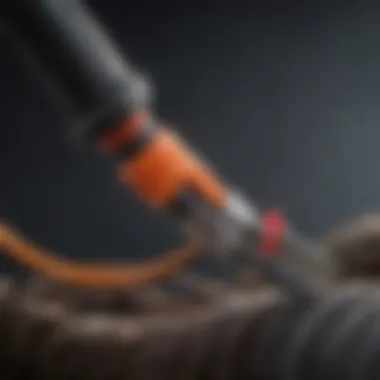
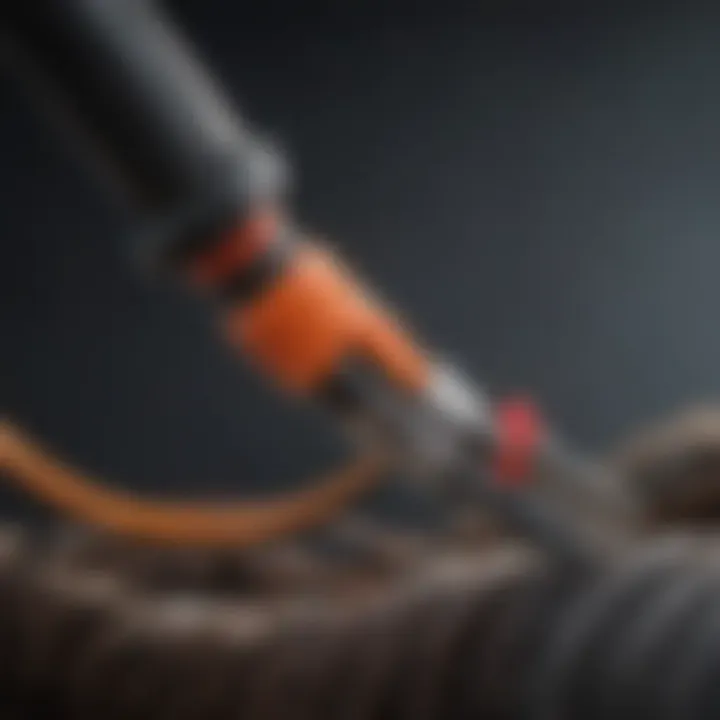
Intro
In the realm of aviation and engineering, the choice of materials is critical. One such material is the 3 32 aircraft cable, known for its durability and reliability. This article aims to provide an extensive understanding of this specific type of aircraft cable, covering its specifications, various applications, and best practices for safe use across industries. We will delve into the properties that characterize 3 32 aircraft cable, outline installation techniques, and discuss maintenance protocols to ensure its longevity.
Whether you are involved in the manufacturing, installation, or maintenance of aircraft systems, understanding the key aspects of 3 32 aircraft cable is vital. By grasping the intricacies of this cable type, professionals can enhance safety protocols and operational efficiency. Let's explore further.
Overview of Aircraft Cable
3 32 aircraft cable plays a critical role in various industries, notably aviation and construction. Understanding this type of cable helps not only in selection but also in ensuring safety and structural reliability. This section will examine its definition, composition, and physical properties, as well as the applicable standards and regulations.
The significance of 3 32 aircraft cable cannot be understated. It serves as a fundamental component in several applications, where strength and flexibility are paramount. By gaining insight into its attributes, users can make informed decisions about its applications.
Definition and Composition
3 32 aircraft cable consists of several strands of wire twisted together, resulting in a product known for its strength and durability. Typically, the "3 32" designation refers to the configuration of the cable. This means there are three strands, with each strand containing 32 wires.
The materials used in constructing these cables generally include stainless steel or galvanized steel. This selection ensures resistance to corrosion and allows the cable to endure challenging environments. Knowing the composition helps users in identifying suitability for specific projects, especially where environmental factors influence performance.
Physical Properties
The physical attributes of 3 32 aircraft cable are essential for its effective use. Its diameter usually sits around 3/32 of an inch, providing a lightweight solution without compromising strength. The flexibility of the cable allows for easier handling and installation in various settings. Moreover, the twisting of the strands contributes to its strength, preventing kinks or breaks during operation. The layout of the wires also aids in minimizing fatigue and wear, making it ideal for repeated use over time.
Common Standards and Regulations
Like many industrial components, 3 32 aircraft cable is subject to numerous standards and regulations. These guidelines ensure that the cable can withstand specified loads and perform adequately in different applications. Agencies, such as the American Society for Testing and Materials (ASTM) and the Federal Aviation Administration (FAA), establish these standards.
Compliance with these regulations is non-negotiable, particularly in sectors where safety is paramount, such as aviation. Adhering to these rules not only assures performance but can also mitigate risks associated with cable failure. Understanding these standards provides a framework for evaluating the quality and reliability of 3 32 aircraft cable, aligning it with the necessary safety protocols.
Always consult the latest standards for any updates on material specifications and usage guidelines to maintain compliance and safety.
Applications of Aircraft Cable
The utility of 3 32 aircraft cable spans various industries, showcasing its resilience and adaptability in demanding environments. Understanding the specific applications of this cable is crucial as it directly influences efficiency and safety in operations. Its features provide distinct advantages that cater to the needs of different sectors, making it a vital component in several applications.
Aerospace Industry
In the aerospace sector, 3 32 aircraft cable is integral to many systems. It is used extensively in aircraft control systems, ensuring precise movement and safety. The cable’s high tensile strength and lightweight properties make it ideal for applications where reducing weight is essential without compromising safety. The strict standards in aviation, such as FAA regulations, necessitate cables that can withstand significant stress and environmental factors. Thus, the 3 32 aircraft cable becomes a reliable choice for avionics and equipment that require both robustness and reliability.
Construction and Rigging
Construction also heavily relies on the benefits of 3 32 aircraft cable. In rigging applications, the cable provides support in lifting and securing loads. Its flexibility allows for various configurations, which is essential in dynamic environments like construction sites. Load capacity is a key consideration here; the cable's robust design ensures it can handle significant weight, which is crucial for safety in lifting operations. Proper hardware selection, compatible with 3 32 cables, ensures that the overall rigging system functions effectively and safely.
Maritime Uses
The maritime industry benefits from the durability of 3 32 aircraft cable, particularly in applications like mooring and towing. The cable is resistant to corrosion from seawater and can endure the harsh conditions found at sea. This adaptability is vital for tasks such as securing vessels during docking or handling heavy loads onboard. Furthermore, the cable’s resistance to environmental factors means it requires less frequent replacement, leading to cost savings in the long run. Selecting the right specifications for specific marine applications can optimize performance and enhance safety.
General Industrial Applications
In general industrial settings, 3 32 aircraft cable finds usage in overhead lifting, material handling, and even as part of safety systems. Its versatility ensures that it fits various mechanisms and machines across different industries. The maintenance of systems utilizing this cable is straightforward, allowing for efficient operations. Proper inspection routines ensure that wear and tear are identified early, preventing potential failures. This proactive approach, combined with the cable's inherent strength, maintains operational integrity across many applications.
The applications of 3 32 aircraft cable are broad and essential across many sectors, emphasizing its importance in providing safety and support when needed most.
Technical Specifications of Aircraft Cable
Understanding the technical specifications of 3 32 aircraft cable is crucial for optimal usage in various applications. These specifications outline important factors, such as load capacity and material properties, that directly affect performance and safety. Thus, it is essential for users to become familiar with these details to ensure proper selection and application.
Diameter and Load Capacity
The diameter of 3 32 aircraft cable is typically 3/32 inches, which plays a significant role in determining its load capacity. Load capacity refers to the maximum weight the cable can withstand without risking failure. It is measured in pounds and varies depending on the specific material and construction of the cable.
A few main points to consider regarding diameter and load capacity include:
- Safety Margin: Always account for a safety margin when calculating the load capacity. This prevents overloading and ensures the cable can handle unexpected stresses.
- Application Requirements: Different applications may require specific load capacities. Aircraft cables must meet or exceed the demands placed on them in their respective environments.
- Regular Testing: Conduct thorough testing of your cables periodically to ascertain their effectiveness and safety under various loads.
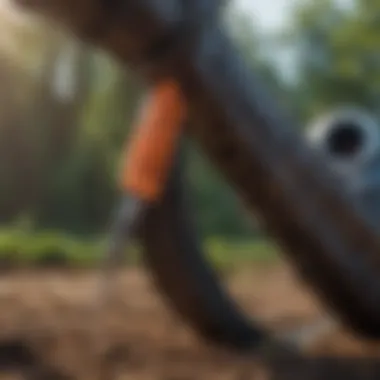
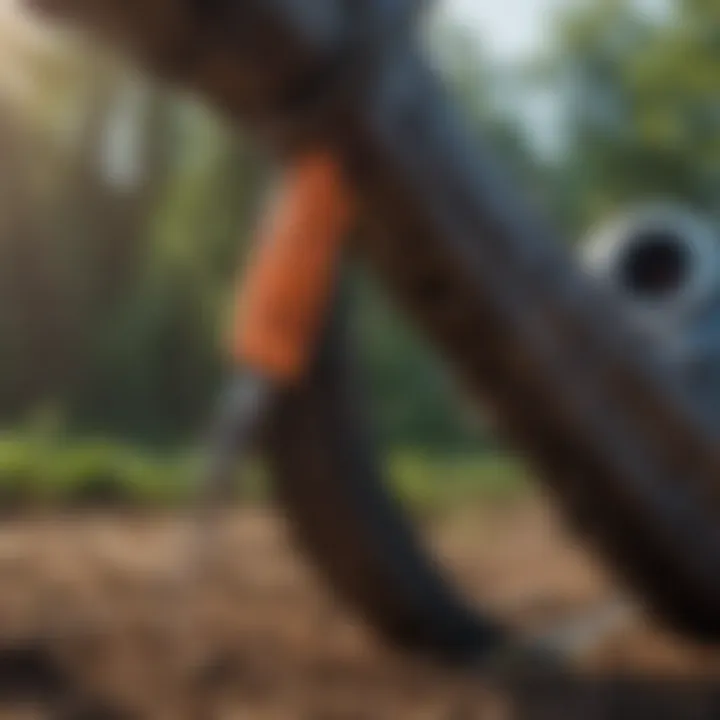
Material Variants and Their Properties
3 32 aircraft cable is manufactured from various materials, primarily stainless steel and galvanized steel. Each material variant carries unique properties that can influence performance and maintenance requirements.
For instance:
- Stainless Steel: This variant is highly resistant to corrosion, making it ideal for applications exposed to harsh environments. Its longevity is significantly higher than other materials, ensuring durability.
- Galvanized Steel: This offers protection against moisture and rust due to its zinc coating. While it is less resistant to corrosion than stainless steel, it is often more cost-effective for projects where exposure to elements is limited.
Understanding these material properties is vital for making informed decisions based on environmental conditions and application needs. Proper material selection can greatly enhance cable longevity and reliability.
Tensile Strength and Durability
Tensile strength is another critical specification of 3 32 aircraft cable. It refers to the maximum amount of tensile (pulling or stretching) stress that the cable can endure before breaking. High tensile strength indicates better performance under tension, making it a desirable feature in many applications.
Durability also links to tensile strength. The ability of the cable to withstand wear and tear over time impacts safety and cost. Items to consider in tensile strength and durability include:
- Cross-Sectional Area: A larger cross-section typically provides greater tensile strength, enhancing load-bearing capabilities.
- Environmental Resistance: Cables designed to resist environmental factors such as UV exposure, chemical reactions, and abrasion will have better durability over the long term.
- Regular Inspections: Conducting regular inspections and checks for wear can help identify issues before they lead to cable failure.
In summary, the technical specifications of 3 32 aircraft cable serve to inform users about its capabilities and limitations. Knowledge of diameter, load capacity, material variants, tensile strength, and durability aids in selecting the right cable for various demanding applications.
Installation Considerations
The process of installing 3 32 aircraft cable is crucial for its effectiveness and safety. Proper installation ensures that the cable functions as intended under varying conditions. A focus on installation considerations helps to prevent future issues and ensures optimal performance in real-world applications.
Choosing the Right Hardware
It is important to choose hardware that is compatible with 3 32 aircraft cable. The selection of fittings, connectors, and fasteners can greatly affect the installation process and the overall integrity of the system. Compatibility can influence the ability of the cable to handle load and resist environmental stressors. Here are a few critical points to consider:
- Material Compatibility: Ensure that hardware materials are robust and suitable for the aircraft cable's environment. Using stainless steel or corrosion-resistant materials is often best in various applications.
- Load Ratings: Always check the load ratings of the hardware. It should match or exceed the load capacity of the cable to prevent failure.
- Ease of Use: Hardware should facilitate straightforward installation processes. Select hardware that is designed for the specific application to reduce installation time.
Proper Installation Techniques
The techniques used during installation play a significant role in the performance of 3 32 aircraft cable. Following standardized installation practices can minimize errors and enhance durability. Key practices include:
- Correct Preparations: Before installation, inspect all components for damage or defects. Ensure that the area is clear and safe for working.
- Secure Tensioning: Properly tensioning the cable is essential. Use calibrated tools to achieve the right tension, preventing sagging which could lead to cable fatigue.
- Follow Manufacturer Guidelines: Always adhere to any guidelines provided by manufacturers regarding installation practices. This reduces the risk of issues stemming from improper setups.
Safety Precautions During Installation
Safety should always be a priority during the installation process of 3 32 aircraft cable. Taking precautions can protect both the installer and the integrity of the installation itself. Here are some vital safety tips:
- Personal Protective Equipment (PPE): Use appropriate PPE including gloves, safety glasses, and helmets. This minimizes the risk of injury from sharp cable ends.
- Worksite Safety Measures: Keep the work area tidy and free from debris. Establish barriers if necessary to protect those working in the vicinity.
- Team Coordination: If working in teams, communication is crucial. Ensure everyone is aware of their roles and the installation plan.
Following these installation considerations significantly reduces risks associated with the usage of 3 32 aircraft cable. Comprehensive planning and awareness lead to safe and efficient operational outcomes.
Maintenance and Inspection Practices
Maintenance and inspection practices are crucial for ensuring the safety and longevity of 3 32 aircraft cable. A well-maintained cable reduces the likelihood of failure, which can lead to serious accidents in various applications. Regular checks help in identifying minor issues before they escalate into major repair needs. It is not only about routine maintenance but also about understanding the overall health of the cable, which directly impacts its performance and reliability.
Routine Inspection Routines
Establishing a routine inspection process is essential. Inspections should be done regularly to ensure that the aircraft cable remains in optimal condition. Key elements in this routine include:
- Visual Inspection: Check for fraying, kinks, or signs of corrosion on the cable.
- Load Tests: Conduct load tests if applicable, to assess its capability under working conditions.
- End Fittings Check: Inspect the end fittings for any signs of wear or stress.
- Documentation: Keep detailed records of each inspection, noting any findings and actions taken.
Routine inspections should be scheduled based on the cable's usage frequency. For cables used in critical applications, more frequent inspections may be warranted. It helps to ensure that any anomalies are detected early and addressed promptly.
Identifying Wear and Tear
Recognizing the signs of wear and tear can prevent more significant issues down the line. Key indicators to look for include:
- Broken strands: The appearance of broken or missing strands is a serious flag.
- Corrosion: Rust or corrosion can weaken the material and should be addressed immediately.
- Abnormal Stretching: Any unusual elongation may indicate an overload or weakening of the cable.
Regularly educating team members about these signs can promote a proactive approach to maintenance. Early detection often leads to easier, less costly repairs.
Maintenance Tips for Longevity
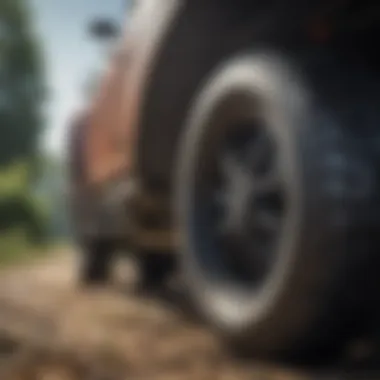
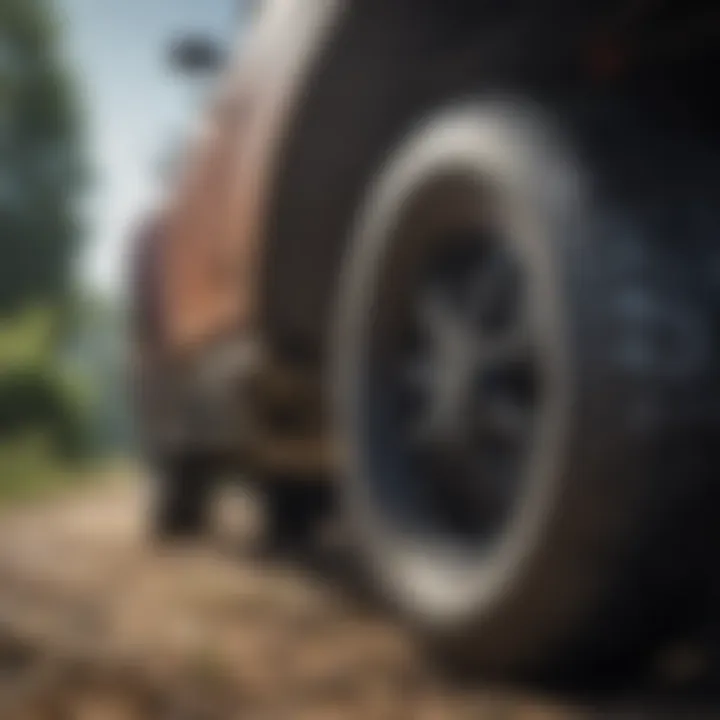
To ensure the longevity of the 3 32 aircraft cable, consider these maintenance tips:
- Cleaning: Keep cables clean and free from any debris or harmful substances.
- Proper Storage: Store cables in a cool, dry place when not in use. Avoid coiling them tightly to prevent deformation.
- Environmental Considerations: Be aware of the environmental factors that could affect the cable, such as extreme temperatures or exposure to chemicals.
- Periodic Lubrication: If appropriate, lubricate moving parts or connections to reduce friction and wear.
Regular maintenance not only extends the lifespan of the cable but also enhances safety. Effective practices can make all the difference in operational efficiency.
By taking these practices seriously, one can ensure that 3 32 aircraft cables remain safe, efficient, and effective for their intended applications.
Troubleshooting Common Issues
Troubleshooting common issues related to 3/32 aircraft cable is a critical aspect of maintaining high safety standards and operational efficiency. Identifying and resolving problems ensures that cables perform as they should under load, which is especially important in industries such as aerospace, construction, and maritime activities where safety cannot be compromised. This section delves into key failure indicators and resolution approaches, equipping users with the knowledge to tackle potential issues effectively.
Common Failure Indicators
Various indicators can signal potential problems with 3/32 aircraft cables. Recognizing these signs early can prevent accidents and costly downtime. Common failure indicators include:
- Fraying or Worn Sections: Visible wear on the surface of the cable may suggest that it has been exposed to excess friction or extreme environmental conditions.
- Kinks or Twists: Permanent kinks or twists in the cable disrupt its integrity. They can lead to increased stress and eventual failure.
- Corrosion: Especially for cables used in marine environments, corrosion can weaken the cable over time. Inspect for rust or other forms of deterioration.
- Reduction in Load Capacity: If cables are used beyond their specified load limits, they may exhibit signs of failure and should be inspected thoroughly.
- Sound Changes: Unusual noises during operation could indicate internal damage or failure in cable systems.
"Early detection is key. Regular inspections can catch signs of failure before they escalate."
Resolution Approaches
Once failure indicators are identified, it is essential to take appropriate measures for resolution. The approaches may vary depending on the severity of the issue:
- Regular Inspections: Conduct visual and tactile inspections periodically to identify potential issues. Cracked, frayed, or corroded sections should be replaced immediately.
- Retensioning: If a cable has become too loose over time, retensioning may restore its operational capacity. Use proper tensioning tools to ensure accurate adjustments.
- Replacement: For cables that show significant wear or damage, replacement is the most reliable option. Ensure the new cable meets appropriate specifications for safety and efficiency.
- Repair Techniques: In some cases, especially with minor kinks or twists, specialized techniques such as splicing may alleviate the issue. However, this is best left to professionals.
- Adjusting Usage: Evaluate and adjust the operational parameters to better suit the capabilities of the 3/32 aircraft cable. Avoid exceeding load limits to prolong the cable's lifecycle.
Understanding these indicators and resolution methods ensures that users of 3/32 aircraft cable can maintain optimal performance and safety, ultimately supporting their operational demands.
Advantages of Using Aircraft Cable
The decision to utilize 3 32 aircraft cable brings with it various advantages that are crucial across numerous sectors. These cables, known for their unique characteristics, provide significant benefits in performance, safety, and longevity. Understanding these advantages can aid in informed decision-making about material choice, especially for applications requiring reliable strength and durability.
Weight to Strength Ratio
One of the most compelling advantages of 3 32 aircraft cable is its exceptional weight to strength ratio. This characteristic ensures that the cable can handle substantial loads without adding excessive weight. In industries such as aerospace and construction, where weight savings are critical, the reduced mass of the cable helps improve fuel efficiency and overall performance.
The use of high-strength steel alloys in the construction of 3 32 aircraft cables contributes to this advantageous ratio. This design allows the cable to support weighty applications while remaining manageable and easy to handle. Engineers and suppliers often recommend this cable for tasks involving heavy lifting or load-bearing, as it strikes an optimal balance between strength and weight.
Resistance to Environmental Factors
Another notable feature of 3 32 aircraft cable is its resistance to various environmental factors. This resistance is particularly important in applications exposed to harsh conditions, such as marine environments or outdoor settings.
3 32 aircraft cable is often treated with protective coatings to enhance its durability against corrosion, humidity, and UV exposure. This resistance not only prolongs the lifespan of the cable but also reduces maintenance costs over time.
Furthermore, its performance is reliable even in extreme temperatures, making it suitable for use in diverse climates. As a result, for industries such as maritime operations or outdoor construction projects, 3 32 aircraft cable is an excellent choice due to its resilience and ability to withstand environmental stressors.
3 32 aircraft cable combines high tensile strength with low weight and excellent durability against environmental factors, making it a preferred choice across multiple applications.
Through understanding these advantages, users can appreciate the distinctive qualities offered by 3 32 aircraft cable. These strengths highlight why the cable is often selected as a primary material in various demanding applications.
Comparing Aircraft Cable with Other Options
In the selection process for aircraft cables, understanding the differences between options like steel and aluminum is vital. Each material has its unique properties, making it suitable for varied applications. Moreover, a thorough cost analysis can impact decisions made by businesses in different sectors.
Steel vs. Aluminum Cables
When comparing steel and aluminum cables, we can see distinct advantages and disadvantages. Steel cables generally offer superior strength. They have a higher tensile strength compared to aluminum. This means they can handle more weight and stress before failing. For many applications in the aerospace and heavy construction industries, this robustness is crucial. However, steel cables are heavier. This added weight can be a limitation in certain scenarios where weight reduction is a priority.
Aluminum cables, on the other hand, are known for their lighter weight. This makes them an appealing option for applications that require easy handling and transport. The reduction in weight doesn’t dramatically sacrifice strength, but it does mean they may not be suitable for all situations. Aluminum is also more resistant to corrosion compared to steel, making it a good choice in harsh environments. This is especially relevant in maritime applications where saltwater exposure is a frequent issue.
Summary of Key Points:
- Strength: Steel cables outweigh aluminum in tensile strength.
- Weight: Aluminum's lightness offers ease of handling.
- Corrosion Resistance: Aluminum provides better durability in harsh conditions.
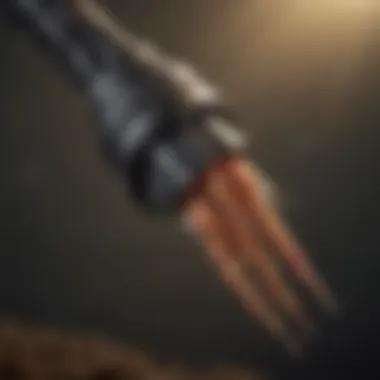
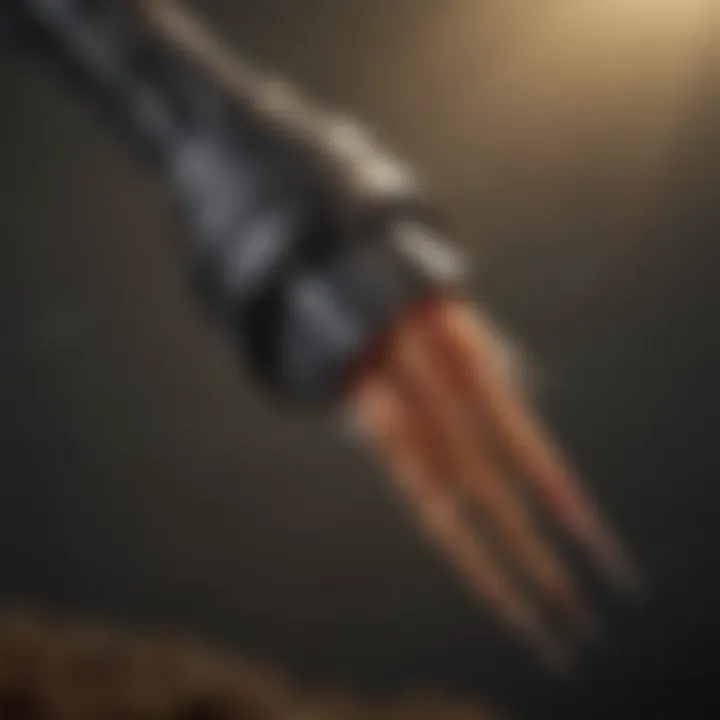
Cost Analysis
Cost is a pivotal factor when deciding between different types of aircraft cables. Generally, steel cables are less expensive to produce. This may make them the preferred choice for companies looking to minimize material costs. However, it is essential to consider the long-term costs of maintenance and potential replacements.
Aluminum cables might come at a higher initial price. Yet, their resistance to corrosion can result in lower maintenance costs and extended service life. Thus, investing in aluminum might be economically viable over time.
A useful strategy for businesses is to compare not only the upfront cost, but also the total cost of ownership. For example:
- Steel Cables: Lower initial cost, but potential for higher maintenance over time.
- Aluminum Cables: Higher initial investment, lower maintenance costs, and longer lifespan.
Ultimately, the decision hinges on the specific requirements of the application, the environment in which the cables will operate, and the budget constraints of the company.
"Choosing the right aircraft cable involves understanding the trade-offs between cost, weight, strength, and environment suitability."
In the world of 3 32 aircraft cable, this analysis aids in making informed choices. Knowledge of the differences in materials and costs empowers industries to optimize their operations effectively.
Future Trends in Aircraft Cable Use
The landscape of aircraft cable usage is witnessing significant transformations due to technological advancements and evolving industry demands. Understanding the future trends in aircraft cable use is critical, especially for professionals in the aviation and related sectors. This section delves into two main aspects that are shaping the future: innovations in material science and the increased automation in installation processes. These elements not only offer enhancements in performance but also ensure better safety and efficiency.
Innovations in Material Science
Material science is at the forefront of improving the effectiveness and resilience of 3 32 aircraft cable. New materials, often stronger and lighter than traditional options, are being developed to meet rigorous performance requirements. The advent of composite materials is particularly noteworthy; these materials provide superior strength-to-weight ratios and improved fatigue resistance, essential for the demanding conditions aircraft cables encounter.
Researchers are also exploring the use of advanced coatings. These coatings can enhance resistance to corrosion and wear, extending the lifespan of cables and reducing maintenance costs. The integration of sensors into the cables might be another future innovation. These smart features can monitor the condition of the cable in real time, alerting operators to potential issues before they escalate into safety hazards.
Key Benefits of Innovations in Material Science:
- Improved strength and durability
- Increased resistance to environmental factors
- Potential for real-time monitoring
This focus on material advancements signifies a vital evolution in ensuring that 3 32 aircraft cables are not only robust but also suited for future aviation needs.
Increased Automation in Installation
The trend towards automation in installation processes is transforming how 3 32 aircraft cables are incorporated into various systems. Automation reduces the time and effort required for installation, significantly enhancing efficiency. It also minimizes human error, which is paramount when dealing with materials that will be subjected to high stress and demand strict compliance with safety regulations.
Employing robotics and automated machinery in installation can ensure greater consistency in cable assembly and alignment. This level of precision is crucial for maintaining performance standards and prolonging the lifespan of the cables.
Considerations with Increased Automation:
- Need for skilled operators to oversee automated systems
- Initial investment costs for automation technology
- Long-term cost savings through efficiency gains
The increased automation trend not only promotes safety but also aligns with broader industry movements towards digitization and smart technologies. This ensures that aircraft cables remain reliable components in modern aviation applications.
"The future of aircraft cable use hinges on material innovations and automation, setting new benchmarks for safety and operational efficiency."
Continued attention to these trends will help industry professionals stay ahead, maintaining the reliability and performance that 3 32 aircraft cables are known for.
Culmination
The conclusion of an article on 3 32 aircraft cable serves as the final touchpoint for readers, encapsulating the critical insights drawn from the discussions in previous sections. It is vital to synthesize the information on specifications, applications, and best practices while also reiterating the relevance of 3 32 aircraft cable in various industries. By understanding its features and functions, professionals can make informed decisions that enhance safety and operational efficiency in their respective fields.
Overall, this section highlights key elements like construction, material properties, installation techniques, and maintenance practices—factors essential for effective usage. The significance of these details lies in their practical application. By adhering to outlined best practices, users can extend the lifespan of the cable and reduce the risk of failures during critical operations.
Recap of Key Points
Throughout the article, several important aspects of 3 32 aircraft cable have been detailed:
- Definition: 3 32 aircraft cable is special cable designed for high strength and lightweight applications.
- Applications: It is widely utilized across aerospace, construction, maritime, and general industrial sectors.
- Installation Guidelines: Proper techniques and selection of hardware are crucial for installation success.
- Maintenance: Routine inspections and addressing wear and tear increase longevity.
- Troubleshooting: Knowing how to identify and resolve common issues ensures safety and effectiveness.
This recap serves as a reminder of the foundational elements that underscore the relevance of 3 32 aircraft cable in today's complex environments.
Importance of Proper Selection and Usage
Making the right choice when selecting 3 32 aircraft cable is critical. The correct selection impacts efficiency, safety, and overall performance of the applications in which the cable is used. For example, one must consider the specific load capacities specified by manufacturers to ensure that any weight-bearing operations are performed safely.
Furthermore, understanding proper usage practices ensures that the cable performs optimally throughout its lifespan. Such practices include:
- Following the manufacturer's installation instructions
- Conducting regular inspections for signs of wear or damage
- Using appropriate equipment for handling and installation
In summary, proper selection and consistent usage of 3 32 aircraft cable enhance its reliability in demanding conditions, thereby reducing risks and operational downtimes.