Miller Arc Welder Generator: A Complete Overview
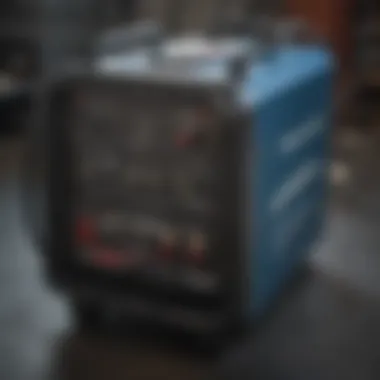
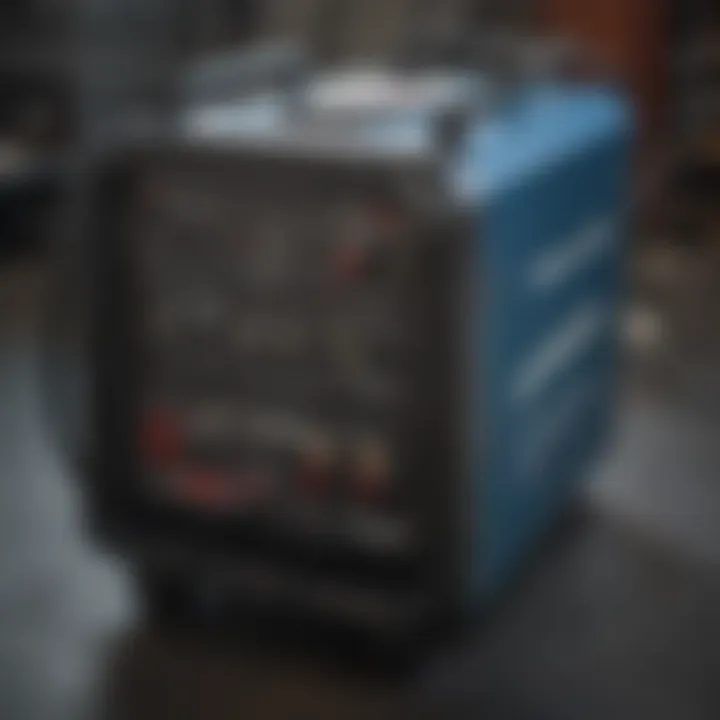
Intro
As the agriculture industry evolves, so too do the tools and techniques utilized by farmers and horticulturists. Among these tools, the Miller Arc Welder Generator stands out as a vital piece of equipment. Whether it's for metal repairs on farming machinery or for creating custom metal structures, understanding this generator can significantly enhance farming practices.
This article aims to provide an in-depth look at the Miller Arc Welder Generator, touching on its operational mechanics and benefits, particularly in agricultural settings. As the demand for efficient and sustainable farming increases, having reliable tools becomes paramount.
Current Trends in Agriculture and Horticulture
The landscape of agriculture is changing rapidly, with newer technologies and sustainable practices shaping how crops are grown and maintained.
Overview of Recent Innovations
Today, farmers are increasingly relying on technology to optimize productivity and ensure soil and crop health. Innovations such as precision agriculture tools, drones for monitoring crop conditions, and advanced irrigation systems have become commonplace. The Miller Arc Welder Generator fits well into this picture, offering structural solutions on-site, enhancing efficiency compared to traditional welding methods.
Sustainable Practices Gaining Popularity
Adopting eco-friendly methods isn’t just a trend; it’s becoming a necessity. More farmers are turning to sustainable practices for several reasons, including cost savings and environmental impact. For instance, using solar-powered generators, like the Miller Arc Welder, aligns with this shift. Not only does it reduce dependency on fossil fuels, but it also allows for mobility and flexibility in tough farm environments.
Essential Farming Techniques
To improve productivity, farmers are continually refining their techniques. Understanding how tools like the Miller Arc Welder Generator can aid in this process is crucial.
Soil Health Management
Healthy soil is the backbone of successful farming. Techniques such as crop rotation and cover cropping support soil health and minimize erosion. The role of welding generators becomes evident when repairing or constructing fencing or infrastructure, which is essential for better soil management.
Pest and Disease Control Strategies
Effective pest control is vital to sustainable agriculture. Integrated Pest Management (IPM) is a widely accepted method. The Miller Arc Welder allows farmers to create customized traps or barriers, further enhancing their pest control strategies.
Tools and Technology in Farming
Embracing technology is no longer just for large-scale operations; even small farms can benefit significantly.
Overview of Advanced Farming Tools
From autonomous tractors to wireless sensors, the farming industry is embracing innovations that enhance operational efficiency. The Miller Arc Welder Generator serves as a tool that complements this advancement, providing the means for immediate repairs or fabrications right on the farm.
Case Studies on the Use of Technology
Several successful farmers have incorporated welding techniques using generators into their daily operations. One farmer in California has used the Miller Arc Welder Generator to repair farm equipment promptly, reducing downtime significantly. This not only allows for better productivity but also saves on repair costs in the long run.
"Utilizing modern tools and technologies is not just about following the trend; it’s about ensuring sustainable and successful practices in farming."
As we delve deeper into the operational mechanisms and applications of the Miller Arc Welder Generator, it becomes evident that knowing how to effectively use this tool can lead to significant improvements in agricultural practices. Let’s explore its advantages and safety considerations next.
Prologue to Miller Arc Welders
When venturing into the realm of welding, particularly for agriculture, understanding Miller Arc Welders becomes crucial. These machines are not just tools; they're the backbone of many agricultural processes, allowing for various welding applications that support both equipment and structural integrity in farms. The increasing reliance on these generators underscores their importance in today’s tech-savvy farming environments.
Understanding Arc Welding
At the core of the Miller Arc Welder's functionality is the process known as arc welding. It’s fascinating, really—this method employs an electric arc to melt metal, creating a strong bond between materials. In simple terms, the welder generates a controlled electrical current, which, when bridged between the welding rod and the base metal, creates a high-temperature arc. This heat melts the metals at the joint, enabling them to fuse as they cool down.
Arc welding boasts several methods based on the type of electrode used. The different techniques not only affect the quality of the weld but also the type of materials that can be successfully bonded. Whether one is working with steel, aluminum, or other alloys, understanding the nuances of arc welding could mean the difference between a solid hold and a job gone awry.
Importance in Agricultural Applications
In agricultural settings, the significance of Miller Arc Welders stands out prominently. From repairing heavy machinery to crafting durable farming tools, these welders play a multifaceted role. Here are some compelling reasons why they matter:
- Durability and Strength: Agriculture is tough on equipment. The ability to weld and repair machinery ensures that farmers can maintain their tools for longer, saving costs on replacements.
- Customization: Farmers often need specific tools to meet unique challenges. With the right welding equipment, they can fabricate custom tools tailored for specific tasks, enhancing their operational efficiency.
- Cost Effectiveness: Investing in a Miller Arc Welder can prove to be economical over time. Instead of frequent purchases of new tools or equipment, farmers can repair and repurpose existing assets.
As such, it's clear that understanding the functionalities and applications of Miller Arc Welders is instrumental for anyone in agriculture. Not only does it facilitate better practices but supports overall sustainability in farming. This brings us to the next section, diving deeper into the components that make up the Miller Arc Welder Generator.
Components of the Miller Arc Welder Generator
Understanding the components of the Miller Arc Welder Generator is essential for anyone venturing into the field of welding, especially for those in agricultural settings. Each part plays a pivotal role in ensuring that the machine operates efficiently and safely. By grasping how these components interact, farmers and enthusiasts can make informed decisions about which functionalities best suit their unique needs.
Power Source and Generators
At the heart of any Miller Arc Welder Generator is its power source. This component converts mechanical energy into electrical energy to create the necessary heat for welding. For agricultural applications, where power availability may vary, having a generator that can provide a steady flow of energy is crucial.
Imagine working in a remote field, surrounded by crops yet without an electrical outlet in sight. In such scenarios, the generator not only acts as a backup power supply but enables seamless operation of welding projects like repairing fencing or crafting customized equipment without dependence on a grid supply.
Key aspects to consider when examining the power source include:
- Wattage Output: A powerful generator can tackle thicker materials and more demanding projects.
- Fuel Type: gas or diesel generators have their pros and cons—diesel models often provide longer run times, while gas can be easier to maintain.
- Portability: Given the mobility requirements typical in agricultural tasks, a lightweight design can significantly streamline job processes.
Welding Machinery
The welding machinery component of the Miller Arc Welder Generator incorporates various tools and mechanisms that facilitate the actual welding process. This includes the welding electrode holder, leads, and gas systems for shielding—each plays an indispensable role in achieving quality welds.
In farming, unique welding tasks surface regularly, such as structural repairs on tractors or fabrication of implements. Understanding the welding machinery's specifications heightens the effectiveness of these projects:
- Electrode Size: Depending on the thickness of the materials being joined, selecting the compatible electrode size is key for strong joint integrity.
- Wire Feed Speed: Adjusting this parameter ensures the right amount of material is fed into the weld pool, directly impacting the weld quality.
- Cooling Systems: Efficient cooling mechanisms prevent overheating, ensuring reliability and longevity of the machine, especially during heavy use.
Control Systems
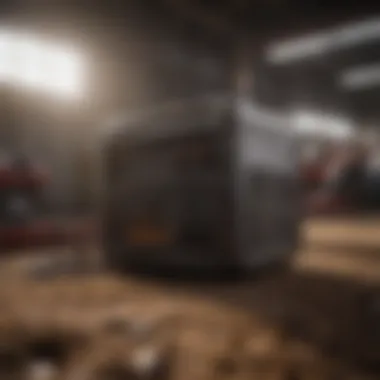
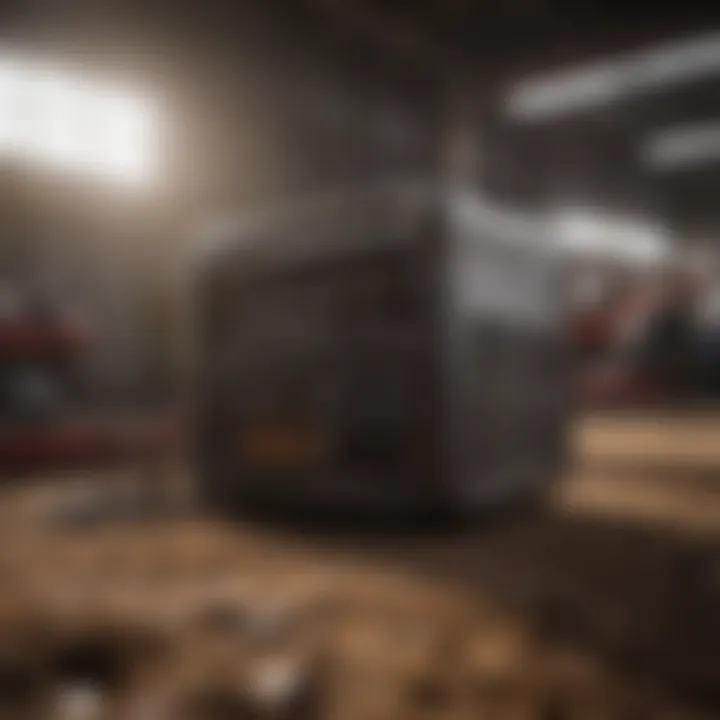
The control systems of Miller Arc Welders may not be immediately visible, but they provide the unseen guidance that directs operations. They regulate everything from arc stability to voltage output, adapting as conditions change. This becomes especially relevant in agricultural applications where external factors, like wind and humidity, can affect welding outcomes.
A sophisticated control system can offer:
- Digital Displays: These allow for real-time monitoring and adjustments, enabling more precise control over the welding parameters.
- Override Functions: In instances where manual intervention is necessary, having these functions can prevent mishaps or equipment damage.
- Memory Settings: For farmers who perform similar tasks often, being able to save and recall specific settings can save time and enhance productivity.
Each of these components has its purpose in the grand scheme of welding. Farmers and welding enthusiasts alike should develop a robust understanding of these elements, ensuring they maximize the utility and efficiency of the Miller Arc Welder Generator. As the agricultural sector becomes increasingly reliant on innovative machinery, acknowledging and leveraging these components lays the groundwork for optimal welding practices within various agricultural contexts.
The combination of power source, welding machinery, and control systems defines not just the effectiveness of a Miller Arc Welder Generator, but its suitability for the demanding conditions of agricultural tasks.
Operational Mechanisms
Understanding the operational mechanisms of the Miller Arc Welder Generator is crucial for anyone involved in welding, particularly in agriculture. These mechanisms influence not only how effectively the welder operates but also the extent to which it can adapt to varying tasks and conditions. At its core, the efficiency of arc welding lies in its ability to produce a strong, reliable weld through a controlled electric arc, and comprehending the nuances behind it can unlock greater potential for users.
How Arc Welding Works
Arc welding can be thought of as a dance between electricity and metal. When the welder initiates the process, an electric arc is generated between the electrode and the workpiece. This arc unleashes intense heat, often exceeding thousands of degrees Celsius, allowing the metal components to melt and fuse together.
- Initiation of the Arc: First, the welder strikes an arc. A starting voltage is triggered that ramps up to a higher voltage to maintain stability.
- Electrical Circuit: The welder creates a continuous electric circuit. This allows current to flow through the electrode, generating heat sufficient to melt both the electrode and base metals.
- Filler Material Addition: In a lot of instances, a filler rod can be introduced into the weld area. This helps enhance joint strength and reduces the risk of material fatigue.
- Cooling Process: Post-weld, the molten material cools and solidifies, forming a strong bond. The heat affects the surrounding material as well, making it crucial to control the heat input to minimize warping or weakening of the base material.
Understanding this intricate process not only demystifies arc welding but also allows operators to manipulate parameters such as voltage and speed for optimal results in varied applications.
Generator Functions
The generator's functions play an indispensable role in the overall welding experience. A robust generator ensures that you have reliable power even during prolonged operations, a crucial consideration in agricultural settings where time is money. There are several key functions to consider:
- Voltage Control: Regulating voltage is essential for both the effectiveness and quality of the weld. It ensures that sufficient heat is produced without overheating the materials.
- Current Regulation: The welder must manage current levels, adjusting for different materials and thicknesses to promote uniform welds.
- Power Output Stability: A generator must deliver stable power output to sustain the arc throughout the welding process. Fluctuations can lead to incomplete or weak welds, which is particularly problematic in agricultural machinery.
- Portability and Setup: Many generators come equipped with features designed for ease of movement and setup. Look for connections and wheels that simplify transportation, especially if the welding will be carried out across extensive fields or various job sites.
The intricate relationship between these functions cannot be overstated. Properly functioning generators are non-negotiable for productive welding, lessening downtime and enhancing the quality of the output.
"Understanding how your Miller Arc Welder Generator operates can be the difference between a job well done and a frustrating workday."
Overall, diving deep into these operational mechanisms equips users with the knowledge to maximize their welding efforts, ultimately delivering superior results efficiently and safely.
Advantages of Miller Arc Welders
When it comes to welding, the Miller Arc Welder Generator stands tall among its peers. With a reputation that precedes it, this equipment provides numerous benefits that cater especially to professionals and hobbyists in the agricultural sector. Understanding these advantages is crucial, as they can greatly influence the decision-making process when investing in welding tools. Here are some of the standout features that make the Miller Arc Welders a go-to choice for many.
Efficiency in Welding
Efficiency isn’t just a buzzword; it’s a vital concern for anyone who engages in welding. The Miller Arc Welder operates with remarkable speed and precision, reducing the amount of time spent on projects. This efficiency is primarily due to its high-performance components which allow for quicker setup and operation.
- Fast Setup and Mobility: Many models are designed with portability in mind, meaning they can be moved from site to site with ease. This means less downtime and more productivity, as workers can get to important tasks without a hitch.
- Consistent Weld Quality: The use of advanced technology helps to ensure that the quality of welds remains high, reducing problems and the need for rework. A welder who can trust their tool's output is a happy welder.
- Fuel Efficiency: Many Miller welders are designed to optimize fuel usage, which is an important consideration for agricultural workers constantly on the move. The ability to get more work done while using less fuel translates directly into cost savings over time.
"A welder who can trust their tool's output is a happy welder."
Versatility Across Different Materials
The versatility of Miller Arc Welders is another reason behind their popularity. These welders don’t just stop at welding steel; they can tackle a multitude of materials. This flexibility makes them an appealing option for agricultural applications where different metal types may be involved.
- Ability to Work with Various Metals: From stainless steel to aluminum, you can count on the Miller Arc Welder to handle a wide range of materials effectively. This is particularly beneficial when farmers need to repair different types of equipment that may be made from various alloys.
- Adapting to Different Thicknesses: Whether you’re working on thin sheets of metal or thicker, more robust sections, these welders can be adjusted accordingly. This adaptability helps to reduce waste and maximize productivity.
- Suitable for Various Techniques: The machine can support different welding techniques like SMAW, GMAW, and FCAW, providing farmers the flexibility to use the method that best suits their needs at any given moment.
These advantages contribute not only to the immediate tasks at hand but also reflect a long-term investment in quality and reliability for agricultural businesses. By understanding the efficiencies and material versatility offered by Miller Arc Welders, potential buyers can make informed choices that will impact their operations positively.
Safety Considerations
When dealing with welding processes, safety isn't just a suggestion; it's essential. In agriculture, where welding has become a crucial part of maintaining and building equipment, understanding safety considerations can spare you from accidents and enhance productivity. The Miller Arc Welder Generator, while a remarkable piece of technology, demands respect and caution. Several specific safety elements must be adhered to for effective and secure utilization of welding equipment. Here, we will explore the critical aspects of protective gear and electrical safety protocols.
Protective Gear Requirements
Welding generates intense heat, light, and sparks. Therefore, protective gear serves as your first line of defense. Equip yourself with the following items to ensure maximum safety while operating the Miller Arc Welder:
- Welding Helmet: A helmet with an appropriate shade lens protects your eyes and face from harmful UV and IR radiation. Look for one with adjustable settings for varied welding applications.
- Gloves: Choose gloves made from heat-resistant materials to protect your hands from burns. The gloves should provide good dexterity while also offering adequate coverage.
- Apron or Protective Clothing: Wear flame-resistant clothing, preferably made from materials like leather or heavy cotton, to shield your body from sparks and molten metal.
- Safety Boots: Steel-toed boots are a must to prevent injury from falling objects, and non-slip soles help maintain stability on uneven surfaces.
- Respiratory Protection: Depending on the type of welding and materials involved, utilizing a respirator can prevent inhalation of harmful fumes.
Keeping this protective gear in check can save a lot of hassle later on. Better safe than sorry, as they say, so ensure it fits well and is maintained regularly.
"The best safety device is a careful worker."
Electrical Safety Protocols
Handling electrical equipment comes with its own set of risks. The Miller Arc Welder operates on significant electrical current, making it vital to follow specific protocols. Here’s what to consider:
- Grounding: Ensure that your welder is properly grounded. An ungrounded welder can lead to dangerous electrical shocks. Check connections frequently, especially in wet conditions.
- Load Management: Avoid overloading circuits when using the Miller Arc Welder Generator. Verify that the power supply meets the welder's specifications to prevent overheating and potential failure.
- Dry Environment: Always use the welder in a dry space. Moisture can increase electrical conductivity, raising the risk of shock. Even minor dampness can lead to accidents, so keeping your work area dry is necessary.
- Inspect Cables: Regularly check power cables for signs of wear or damage. Frayed cables can create serious hazards. If any damage is detected, replace them promptly to ensure safety.
- Disconnect When Not in Use: Unplugging the welder when it's not in operation might seem simple, but it's often overlooked. This practice minimizes risks and prevents accidental starts, especially around other workers.
Prioritize these electrical safety protocols. Knowing how to work carefully with power can make a world of difference in preventing accidents.
Best Practices for Maintenance
Maintaining a Miller Arc Welder Generator is not just a good idea; it's essential for ensuring that the equipment runs smoothly and lasts long. Just like a car needs oil changes and tune-ups, welders require routine care, too. Proper maintenance can enhance performance, prevent unexpected breakdowns, and ensure safety during operation. Ignoring regular upkeep can lead to costly repairs or even dangerous failures. So let’s delve into those best practices that every welder should follow.
Routine Checks and Repairs
Carrying out routine checks is the bread and butter of welder maintenance. Think of it as a ritual. Taking a few minutes to inspect your machine can save heaps of trouble down the line. Here are some crucial aspects to focus on:
- Wiring Inspection: Look for any wear and tear in the wires, considering that even small frays can cause significant electrical issues or even hazards.
- Cooling System: If the welder has a cooling system, it should be checked for clogs or leaks. A well-functioning cooling system prevents overheating, which can damage internal components.
- Electrode Connections: Make sure these are tight and clean, as poor connections can lead to inconsistent welding quality.
- Gas Supply: For those using gas, inspect hoses and regulators for leaks. A quick soapy water test can reveal leaks; if bubbles form, it’s time to replace.
Running a quick inventory of parts every month keeps your welder in top shape. If you spot issues, fix them right away. You don’t want a small hiccup turning into a full-blown crisis when you’re in the middle of a crucial project. A stitch in time saves nine, as they say!
Cleaning Procedures
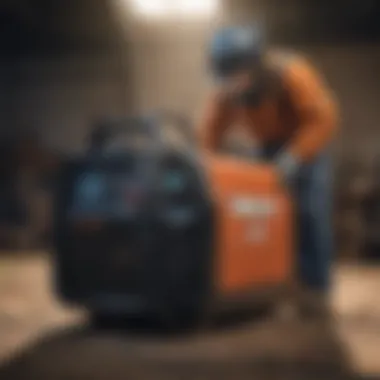
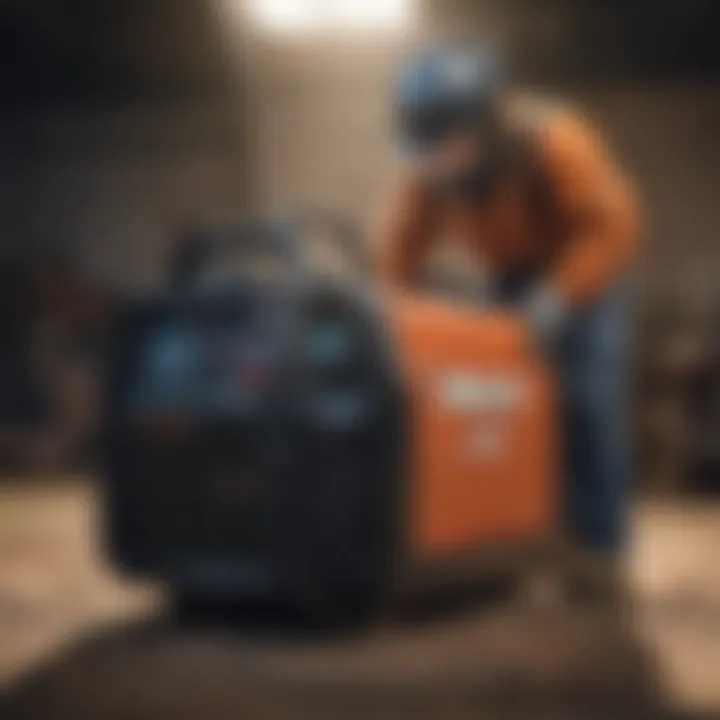
Cleaning is the unsung hero of welder maintenance. Keeping the unit clean not only ensures efficient operation but also prolongs its lifespan. Here’s how to tackle this task:
- Exterior Wipe Down: Dust and debris can accumulate on the outer casing. Use a soft cloth and mild detergent to clean the surfaces, preventing grime buildup.
- Filter Cleaning: If your generator has air filters, clean or replace them regularly. Clogged filters can hinder airflow, leading to overheating.
- Internal Inspection: Once in a while, it’s prudent to open the welder (following safety protocols) to check for dust and dirt accumulation inside. Use compressed air to blow out any dust without damaging internal components.
- Avoid Water: Never use water directly to clean electrical components. This can cause shorts or even permanent damage.
When cleaning, always refer to the manufacturer's instructions. Each machine may have nuances that need addressing.
"A clean machine is a happy machine."
This simple saying holds true, especially in welding. Keeping everything spick and span means your generator will perform when you need it most.
Comparative Analysis with Other Welding Techniques
In any discussion surrounding welding technologies, it's key to understand how different methods measure up against one another. A comparative analysis not only highlights each technique's distinctiveness, but also assists welders, especially in agricultural settings, in making informed decisions tailored to their specific needs.
Arc welding, particularly the Miller Arc Welder Generator, stands as a prominent choice among various welding techniques. But how does it hold up against alternatives like TIG and MIG welding? Let’s take a closer look.
TIG vs. MIG Welding
Both TIG (Tungsten Inert Gas) and MIG (Metal Inert Gas) welding have carved out their respective niches in the welding realm. Here’s a breakdown of their characteristics and how they contrast with Miller Arc Welding:
- Skill Level:
- Application:
- Material Versatility:
- TIG Welding: This method requires a higher skill level. The welder controls both the heat and the filler rod simultaneously, which can be quite a juggling act. For those experienced, however, it can deliver pristine results.
- MIG Welding: Easier to learn compared to TIG, making it a more popular option for less experienced welders. The wire feed takes care of a lot, so you can focus on controlling the weld.
- TIG Welding: It shines in scenarios that demand precision, such as intricate parts or thin materials. It’s favored in aerospace and automotive industries for this reason.
- MIG Welding: On the other hand, it’s better suited for general fabrication, particularly in thicker materials, due to its speed and efficiency.
- TIG Welding: Handles a wide array of materials including titanium and aluminum, but it's slower at layering.
- MIG Welding: Great for steel and is quite effective on aluminum as well, making it versatile for many agricultural applications.
In the end, while TIG offers finesse, MIG provides an edge in speed and simplicity. The Miller Arc Welder Generator finds itself bridging the gap, offering robust capabilities that can outshine these methods under certain conditions, especially when tackling heavier agricultural equipment.
Cost-Effectiveness Considerations
Welding is often less about the upfront costs and more about the long-term value. Let’s break it down with respect to the options available:
- Initial Costs:
- Operational Costs:
- Lifespan and Durability:
- TIG Welding systems can be pricier due to their complexity and the need for high-quality components.
- MIG Welding setups tend to be more affordable, but if you're looking for high longevity and robustness, costs can escalate.
- Miller Arc Welders find a sweet spot, with reasonable pricing relative to their performance and durability in demanding environments like farms.
- While TIG provides refined control, it consumes more time and thus incurs higher labor costs.
- Alternatively, MIG welding is quicker but the potential for weld defects could lead to extra expenses in rectification.
- Miller Arc Welders are efficient, promising savings in operational costs through reduced time on jobs while maintaining high-quality outputs.
- Investing in high-quality welding equipment pays off when it lasts longer, requiring lesser repairs.
- In this domain, Miller Arc Welders stand up proudly, promising durability and reliability, making them a long-term investment that farmers can count on.
"Choosing the right welding technique can greatly influence not just the quality of your results, but also your overall operational efficiency and cost management."
Real-World Applications in Agriculture
When it comes to modern agriculture, machinery plays an indispensable role. Among these tools, Miller Arc Welders shine, facilitating a variety of applications directly relevant to farming operations. These welders not only bolster efficiency but also ensure that farmers can maintain and innovate their equipment with ease. Let’s explore how this technology integrates into everyday agricultural practices, proving to be a linchpin in numerous tasks.
Structural Repairs on Equipment
In any farming setup, wear and tear on equipment is just part and parcel of the job. Structures like tractors, plows, and even conveyor belts go through heavy usage. Here's where Miller Arc Welders prove their mettle.
Welders enable farmers to repair metallic structures that endure harsh conditions – think about the elements, the mud, and the daily grind of agricultural work. For instance:
- Tractor Hitches: A broken hitch can leave a farmer in a lurch, unable to tow critical implements. Welding can quickly restore functionality, offering a way back to work.
- Frame Damage: Whether it's due to hitched equipment or a rough landscape, frames bend. Welding allows quick fixes for that vital piece of kit.
- Metal Repairs: Rust and corrosion on components are common. Instead of replacing entire parts, targeted welding can save time and money.
This ability to perform on-the-spot repairs not only enhances productivity but significantly reduces downtime. Farmers can patch up issues without the hassle and cost of sending equipment out for repair.
Fabrication of Specialized Tools
The beauty of Miller Arc Welders extends beyond mere repairs; they also enable the creation of specialized tools tailored to unique farming tasks. Custom fabrication ensures that farmers have the precise tool they need for their specific challenges.
For instance, in a vegetable farm:
- Custom Cultivators: Rather than relying on generic cultivators, farmers can weld bespoke attachments that suit their soil type and crop specifications.
- Unique Attachments for Harvesting: Creating attachments for harvesting machines can optimize efficiency – a vital aspect during peak harvesting times.
This flexibility of creating personalized tools is instrumental in fine-tuning the farming process, allowing for enhanced productivity and tailored solutions. Custom tools can often outperformance standard ones, leading to better yields and efficient crop management.
These real-world applications underline the practicality of Miller Arc Welders in agriculture. Rather than just being tools, they serve as a bridge connecting traditional farming techniques with modern technological advantages. Harnessing this capability equips farmers not only to sustain operations but also to innovate continuously, pushing agricultural boundaries forward.
"The ability to fix and create on-site not only saves time but also enriches the farming toolbox. It’s about being proactive, not reactive.”
In summary, the Miller Arc Welder is more than just a welding machine; it’s a crucial ally in a farmer’s toolkit, ensuring that they can tackle the challenges of modern farming head-on.
Choosing the Right Miller Arc Welder Generator
When it comes to welding in agricultural settings, selecting the right Miller Arc Welder Generator plays a pivotal role in the success and efficiency of your tasks. Many factors come into play when making this choice—considerations that can mean the difference between a seamless project and a frustrating experience. By understanding what to look for in a welder generator, you ensure that your investment not only meets your current needs but also adapts to future demands. Agricultural work often involves various tasks, from equipment maintenance to custom fabrication, making it essential to choose equipment with versatility and power.
One crucial aspect is the welding output. The amperage output of the welder generator will determine the thickness of materials you can effectively work with. Choosing a generator with suitable amperage ensures you can tackle those heavier jobs without a hitch. Furthermore, integrating portability into the equation can make life a whole lot simpler, especially for farmers who are constantly on the go.
This leads us to key specifications that are critical during the decision-making process.
Key Specifications to Consider
When looking for the right Miller Arc Welder Generator, several specifications should be taken into account:
- Amperage Range: The range will dictate what metal thickness you can weld. Look for models that offer a sufficient range to cover various tasks.
- Duty Cycle: This is the amount of time you can operate your welder in a given period without overheating. A higher duty cycle is often better for longer work sessions.
- Weight and Portability: Depending on your worksite, mobility can be essential. A lighter generator may ease transportation and positioning.
- Set-Up Simplicity: A user-friendly setup process ensures you can jump right into work without fumbling too much with complicated instructions.
"Choosing the right specifications for your welder can enhance productivity significantly. It’s akin to finding the perfect tool for the job—having the right gear is half the battle."
These specifications not only guide your immediate decision but also influence your overall satisfaction and the long-term utility of the equipment. After all, investing in a quality welder generator is a commitment to improving your farming operations.
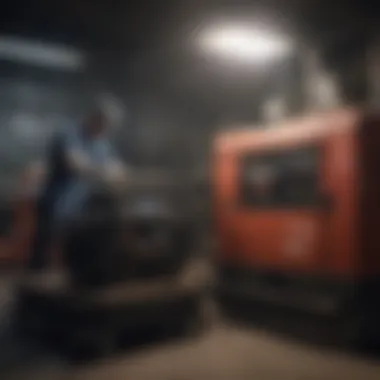
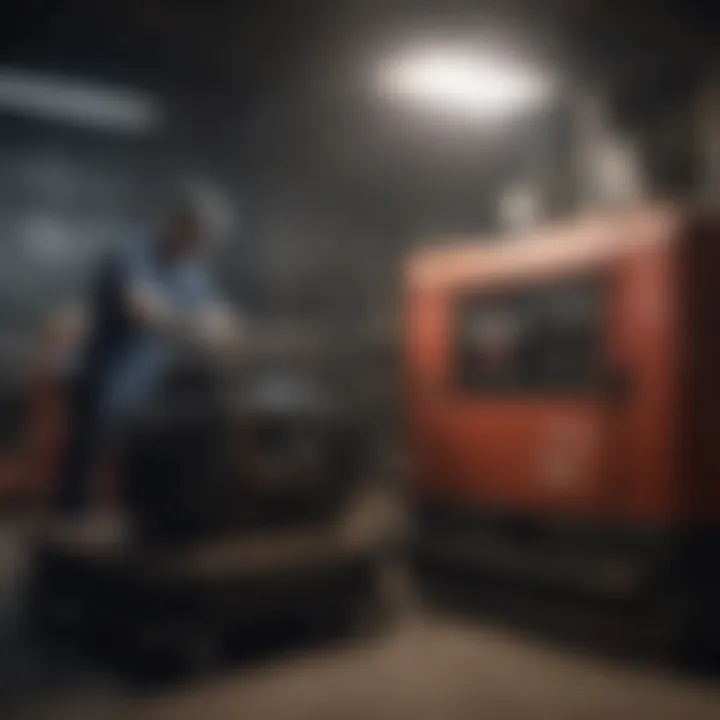
Budgeting for Your Purchase
Finances are always a significant concern, especially in farming. Setting a sensible budget for your Miller Arc Welder Generator requires a careful evaluation of your current and foreseeable needs. While it might be tempting to go for the least expensive option, this could come back to haunt you down the line, especially if you find yourself faced with limits that hinder progress.
When budgeting, consider factors such as:
- Initial Cost: This includes the base price of the generator, shipping, taxes, and any essential accessories.
- Operating Costs: Fuel consumption rates, maintenance needs, and repair costs should factor into the overall budget.
- Long-Term Investment: Look for generators that might have a higher upfront cost but will save you money in the long run due to durability and efficiency.
Allocating funds appropriately and understanding the value propositions at play will go a long way in ensuring you make a purchase that is wise and beneficial. In the end, the right Miller Arc Welder Generator isn’t just about functionality; it’s about enabling your success in your agricultural endeavors.
Common Issues and Troubleshooting
When it comes to operating the Miller Arc Welder Generator, even skilled hands can encounter some bumps along the road. Understanding common issues and knowing how to troubleshoot can not only save time but also ensure optimal performance. Here, we delve into the primary troubles you might face and how addressing these can dramatically affect your welding efficiency.
Identifying and Resolving Welding Problems
Welding problems can create a significant roadblock for anyone relying on their arc welder. Common issues include poor arc stability, excessive spatter, or inconsistent bead appearance. Here are a few areas to assess when troubleshooting:
- Electrode Quality: A worn or degraded electrode can lead to poor performance. Always check the condition and replace as necessary.
- Welding Parameters: Ensure that the settings align with the metal type. For instance, using too high a voltage on thin materials might cause burn-throughs.
- Workpiece Preparation: Contaminants like rust, dirt, or moisture can greatly affect weld quality. A clean surface is non-negotiable.
- Gas Flow Rate: Insufficient shielding gas can lead to porosity in the weld. Adjust the gas flow according to industry specifications.
The key to resolving these issues often lies in your ability to identify them quickly. Regular inspection and maintenance, coupled with an understanding of welding techniques, can alleviate many problems before they develop into more complex challenges.
When to Seek Professional Help
While most welding issues can be tackled with some troubleshooting knobs and bolts, there are instances when it’s best to call in the experts. Here are signs it might be time to seek professional assistance:
- Persistent Problems: If you find that issues like arc blow or outright equipment failure persist despite your best efforts, it’s wise to consult a professional technician.
- Safety Hazards: Equipment malfunction that poses a risk of electric shock or fire should be evaluated immediately. Never compromise on safety.
- Inexperienced Hands: If you or your team lack experience in handling specific materials or advanced techniques, it’s better to rely on a professional than to risk costly mistakes.
- Complex Repairs: Some equipment issues might require specialized knowledge or parts. Attempting a DIY fix can sometimes lead to further damage, costing more in the long run.
Expert intervention can help get your Miller Arc Welder Generator back on track efficiently, ensuring it operates safely and effectively for your needs.
In welding, just like in life, knowing when to ask for help can save you a world of trouble.
Future Trends in Welding Technology
Welding technology is constantly evolving, adapting to the changing needs of industries and embracing advancements that enhance efficiency and precision. In this section, we’ll explore the critical role that future trends play in the landscape of welding, particularly focusing on the innovations spurred by the agricultural sector. As agricultural practices demand better efficiency and sustainability, understanding these trends becomes imperative for farmers and enthusiasts looking to optimize their craft.
Innovations in Arc Welding Equipment
One of the standout advancements in welding technology is the innovation in arc welding equipment. New designs are making these tools not only more powerful but also more user-friendly. For instance, modern Miller Arc Welders come equipped with features such as digital interfaces and smart technology that allows for precise adjustments to be made on the fly. This is crucial in agricultural settings, where often the conditions can be less than ideal.
Advancements like the integration of inverter technology allow for more consistent arcs at lower amperages while using less input power. This equipment becomes more portable, which is a significant benefit for farmers who work with large structures and equipment on varied locations. Indeed, the shift towards lightweight models ensures that even small-scale operators can handle the machinery without needing an army of workers.
Moreover, manufacturers are embracing energy-efficient designs that not only reduce power consumption but also lessen the environmental footprint. If we look at the rise of multi-process welders, they broaden the scope of what a farmer can do. These machines can handle multiple welding processes, from stick welding to MIG and TIG, with ease. This flexibility allows for immediate adaptations to the job at hand without needing a suite of different equipment.
The Shift Towards Automation
The move towards automation in welding is another significant driver of change. Farming itself has been feeling the effects of automation, with larger and more complex machinery requiring specialized skills to maintain. Automated welding solutions can streamline process efficiencies, allowing for quicker project turnaround and reducing the labor intensity traditionally associated with welding tasks.
Automated systems are being developed that focus on robotic welding processes. These systems can handle repetitive tasks consistently and with high precision, which is beneficial for large scale agricultural operations that demand high-volume production. The ability to integrate automated welding machines within larger agricultural frameworks could redefine the efficiency of manufacturing components, from machinery parts to enclosures for farm products.
Furthermore, Machine Learning is also carving out its niche in the welding realm. With intuitive software that can learn from previous welding jobs, these systems can optimize parameters such as speed and heat based on the materials being welded. As these technologies develop, they promise improved outcomes that could significantly reduce material waste and enhance product longevity.
"The welding of the future isn't just about sticking metal together; it's creating holistic solutions for the evolving challenges of industries."
Ultimately, as these trends in innovations and automation meld, they will set a new course for the future of welding, enticing farmers and agricultural stakeholders to embrace these technologies for better functionality and economic savings.
Environmental Considerations
In today’s world, where every industry feels the heat of environmental responsibility, understanding the ecological impact of techniques like welding becomes imperative. When it comes to Miller Arc Welders, recognizing their role in sustainable practices is vital for agricultural professionals and enthusiasts alike. As we dive into this section, we’ll cover both the sustainable welding practices featured in arc welding and what that means for agri-business sustainability.
Sustainable Welding Practices
Sustainable welding practices can significantly reduce the environmental footprint of welding operations. In the context of using Miller Arc Welders, here are few fundamental elements to keep in mind:
- Energy Efficiency: Miller Arc Welders are designed to consume less power while delivering optimal performance. This energy efficiency not only lowers operational costs but also reduces greenhouse gas emissions.
- Material Conservation: Utilizing precise electro-slag welding techniques can minimize the amount of filler and base materials needed. Choosing high-quality materials can lead to lower wastage, an important consideration in agricultural settings where resource conservation matters.
- Emission Control: Implementing effective filtration systems and adhering to strict guidelines on fumes can greatly reduce air pollutants emitted during the welding process. This is crucial not just for the worker's health, but also for the surrounding environment where crops are cultivated.
- Recycling: Reusing scrap metal generated during the welding process can have a double benefit: it reduces costs while promoting sustainable practices. Farms can establish processes to collect excess metal and return it to the market for recycling, thereby closing the loop on waste.
By integrating these practices, farmers can effectively contribute to a healthier ecosystem while maintaining operational efficiency.
Impact on Agricultural Sustainability
The implications of sustainable welding practices extend beyond individual operations to have a profound impact on agricultural sustainability. Here’s how:
"Sustainable agricultural practices lead the path towards ensuring that farming and envrionmental health coexist harmoniously."
- Soil and Crop Health: Welding equipment that minimizes emissions ensures that harmful pollutants do not harm the soil and crops. Healthy soil leads to healthier plants, thus improving overall yields and quality of produce.
- Resource Management: Efficient welding reduces waste, contributing to more sound resource management on the farm. When farmers use resources wisely, they enhance their farming practices while supporting the environment.
- Market Demand: As consumers shift towards sustainably-sourced products, farmers who adopt eco-friendly practices stand to gain a competitive edge. Highlighting the use of sustainable welding practices may attract a clientele that values environmental stewardship.
- Long-term Viability: Practices that focus on sustainability not only protect the immediate environment but also foster long-term viability of the land and farming operations. Ensuring the longevity of resources can sustain farm productivity for future generations.
Epilogue
The conclusion of an article like this serves as a capstone, tying together all the threads woven throughout the various sections. It's crucial to underscore the diverse capabilities of the Miller Arc Welder Generator, not merely as a piece of equipment but as a pivotal instrument that transforms welding practices in agricultural sectors.
As readers reflect on the content presented, it's evident that the discussed advantages—such as efficiency, versatility, and safety—are not just buzzwords. They represent tangible benefits that can enhance productivity and streamline processes in the field. Also, understanding common issues and having a roadmap for troubleshooting ensures that users can operate these machines confidently. The information provided about maintenance best practices reinforces the idea that proper care extends the lifespan of these generators, making them a sound investment over the long haul.
Moreover, the emphasis on environmental considerations brings a vital perspective to the forefront in today’s world, reminding us that the integration of sustainability into our farming methods is not just beneficial but essential. By adopting these welding practices, one not only elevates their operation but also contributes to a broader movement toward sustainable agriculture.
Recap of Key Insights
- Operational Mechanisms: Understanding how the Miller Arc Welder Generator functions is essential. The arc welding process is effective for various materials and applications.
- Safety Protocols: The importance of adhering to safety standards cannot be overstated, ensuring that users are protected while they work.
- Maintenance Practices: Regular checks and cleaning are vital to ensuring that equipment remains in optimal condition.
- Real-World Applications: From structural repairs to the creation of specialized tools, these welders excel in diverse agricultural tasks.
- Environmental Impact: Adopting sustainable welding practices not just benefits individual operations but contributes to the health of our ecosystems.
Call for Continued Innovation in Welding
As the landscape of agriculture continues to evolve, so too must our tools and methodologies. Embracing innovation in welding technology is not merely an option; it is a necessity. The industry is at a juncture where automation and new technologies could redefine capabilities and efficiency. The shift towards more automated solutions can lead to faster processes while maintaining precision and quality.
The call for innovation extends to every aspect of welding—from advancements in welding materials to improvements in power generation methods, every development offers the potential for enhanced performance.
In closing, as farmers and welding enthusiasts seek to harness the capabilities of tools like the Miller Arc Welder Generator, they must remain on the lookout for new technologies and practices that could help push boundaries. The adoption of these innovations will not only assure better results in their immediate tasks but also secure a brighter future for agricultural practices overall.