The Importance of Skinning Cradles in Beef Processing
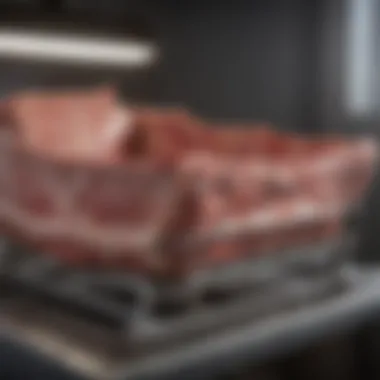
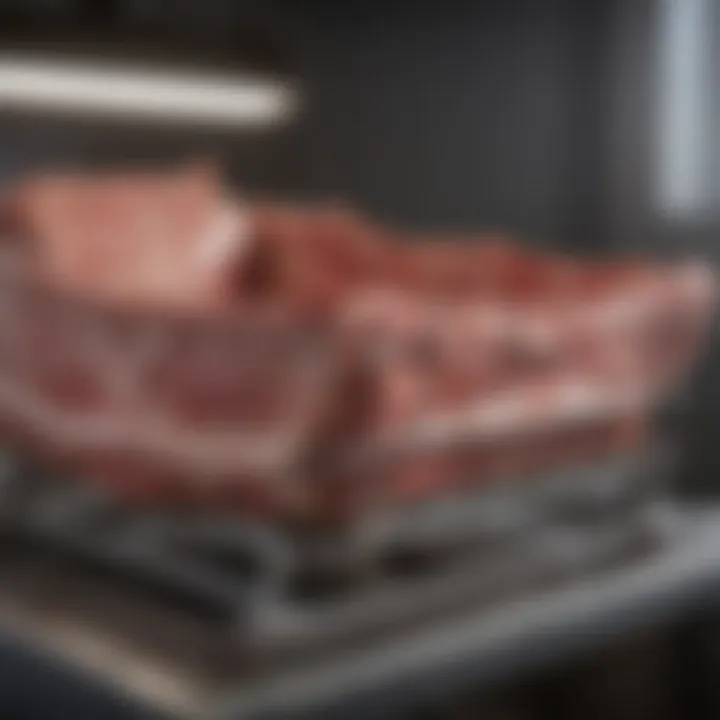
Intro
In the realm of beef processing, a skinning cradle emerges as an indispensable tool, silently working behind the scenes to enhance efficiency and ensure product quality. Often overlooked, these cradles are more than just supports for carcasses; they embody the marriage of traditional techniques and modern operational demands. With the meat industry evolving alongside technological advancements, understanding the importance of skinning cradles is more crucial than ever.
The mechanical and ergonomic design of skinning cradles greatly influences how meat is handled. A skinning cradle not only aids but also transforms the workflow on the production floor. With its ability to facilitate the skimming process, it helps butcher shop workers maintain their pace without compromising quality.
In the following sections, we will discuss how skinning cradles contribute to meat processing, including their design and functionality, and how they play a pivotal role amidst industry trends. Let's delve into the evolving landscape of beef processing and uncover the hidden significance of skinning cradles.
Current Trends in the Meat Processing Industry
Recognizing current trends can help professionals adapt and optimize their operational practices. With an ever-increasing emphasis on efficiency and product safety, the role of tools like skinning cradles is often amplified.
Overview of Recent Innovations
Recent innovations in the meat processing industry reflect a shift towards automation and precision engineering. Skinning cradles, designed with adjustable components, are now being integrated with robotic technologies. Imagine an operational space where human effort is supplemented by machine precision; this makes for a safer and more efficient meat processing environment.
They allow workers to maintain a steady flow while dramatically reducing the physical strain often associated with manual skinning techniques.
Not only are traditional practices a cornerstone of the industry, but they are also being enhanced with modern technology. Equipment is designed not just for performance but also for worker comfort, ultimately promoting a healthier work environment.
Sustainable Practices Gaining Popularity
Sustainability in meat processing is no longer just a buzzword; it's become a necessity. Consumers and operators alike are seeking eco-friendly solutions. Skinning cradles are now crafted with sustainable materials, minimizing their environmental footprint. In addition, practices like waste recycling and energy-efficient operations gain traction, reflecting a broader commitment to sustainability.
The meat industry's shift towards sustainability not only secures its future but also reflects an understanding of consumption trends today.
To align with these shifts, skinning cradles' designs are receiving upgrades to reduce waste while providing the required functionality. As more businesses adopt sustainable practices, cradles become a key component in the quest for a greener solution.
Essential Techniques in Beef Processing
To maximize the benefits of skinning cradles, understanding essential techniques utilized in beef processing is vital. This section outlines the methodologies that professionals in the field apply.
Efficient Skinning Techniques
The skinning process is both an art and a science. Modern cradles enable operators to achieve a clean skinning operation, reducing contamination risks. Best practices include:
- Preparation: Ensure all tools and surfaces are sanitized before commencing skinning.
- Proper Handling: Use hooks and straps effectively to secure the carcass without causing damage.
- Controlled Cuts: Skilled operators apply consistent, controlled movements, promoting quality.
By implementing these techniques, meat processors can significantly enhance product quality and efficiency, while minimizing waste.
Tools and Technology in Meat Processing
The meat processing industry continually embraces new tools and technology to elevate production standards. Understanding how to effectively integrate these tools is crucial.
Overview of Advanced Processing Tools
Skinning cradles represent just one facet of the advanced machinery that modern processors utilize. Clipping machines, automated cut systems, and vacuum technology are all designed to streamline every aspect of the meat processing journey.
Operators who skillfully adapt to these advancements will find themselves better positioned in the competitive market.
Case Studies on the Use of Technology
Various case studies have demonstrated significant improvements in efficiency when technology is introduced into the meat processing domain. For instance, businesses that employed robotic skinning arms alongside traditional cradles saw their production rates increase by 20%, reducing labor fatigue; thus improving conditions for workers.
The End
In summary, the skinning cradle plays a vital role in beef processing, acting as an important facilitator of technological advancement, sustainable practices, and efficient techniques. As operators in the meat processing industry navigate this evolving landscape, understanding and optimizing the use of equipment like skinning cradles will not only enhance product quality but also contributes to a healthier work environment. Embracing these changes can lead to a thriving operation that meets modern demands laid out by consumers and regulatory bodies alike.
Preamble to Skinning Cradles and Their Importance in Beef Processing
Understanding the role of skinning cradles is vital for anyone involved in beef processing. These essential tools are not merely an extra step in the workflow; they are pivotal for maintaining quality and efficiency. Skinning cradles facilitate a smoother transition from livestock to meat product by streamlining the skinning process. This section will explore the nuances of their significance, shedding light on their contributions to improving operational practices in the meat industry.
Overview of Beef Processing
Beef processing is a multifaceted operation that involves several stages, each crucial for ensuring quality and safety. From the moment the animal is received at the processing facility to the point where the final product is packaged, several key processes unfold. Initially, the humane handling of livestock stands at the forefront of modern practices. Once the animal is ready for slaughter, it undergoes various stages such as stunning, bleeding, and eventually skinning. The skinning phase, often seen as a simple act, can greatly impact the meat’s overall quality and yield. Here, skinning cradles step in, turning a labor-intensive task into an organized operation that emphasizes hygiene and precision.
In various settings, processing may differ, but the core principles remain the same. Factors such as temperature control, cross-contamination prevention, and efficient workflow are always front and center. This complex tapestry of activities is where skinning cradles can shine, enhancing the entire processing chain while ensuring that the standards required by food safety regulations are met.
Definition and Purpose of a Skinning Cradle
So, what exactly is a skinning cradle, and why is it essential? A skinning cradle is a tool that supports the carcass during the skinning procedure.
- Functionality: It allows workers to maintain the carcass at an optimal working height, addressing an ergonomic concern that can greatly reduce physical strain during the skinning process.
- Hygiene: Built with materials that are easy to clean, skinning cradles minimize contamination risks, keeping meat safe and up to industry standards.
- Precision: By providing a stable base, they help ensure that the skin is removed efficiently without damaging the underlying tissue, thus preserving more high-quality meat for sale.
Moreover, skinning cradles can vary significantly in design and functionality. There are manual and mechanical options available, each with its own set of advantages and considerations. But regardless of the type, their main goal remains the same: to enhance the efficiency and quality of the beef processing workflow.
"A skining cradle is not just a tool; it is an integral component that bridges the gap between livestock and quality meat products."
In sum, the introduction of skinning cradles into beef processing revolutionizes the industry by addressing various challenges associated with the skinning phase, thus paving the way for a smoother, safer, and more efficient meat processing environment.
Types of Skinning Cradles
In the realm of beef processing, skinning cradles are not merely functional elements; they play a pivotal role in enhancing efficiency, safety, and the overall quality of meat. Understanding the various types of skinning cradles available allows meat processors to choose the right tool for the task at hand. This section delves into the two primary types: manual and mechanical skinning cradles, each bringing its own unique advantages and considerations.
Manual Skinning Cradles
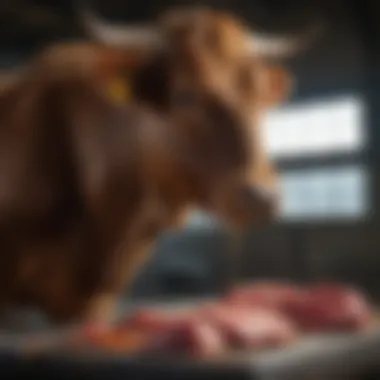
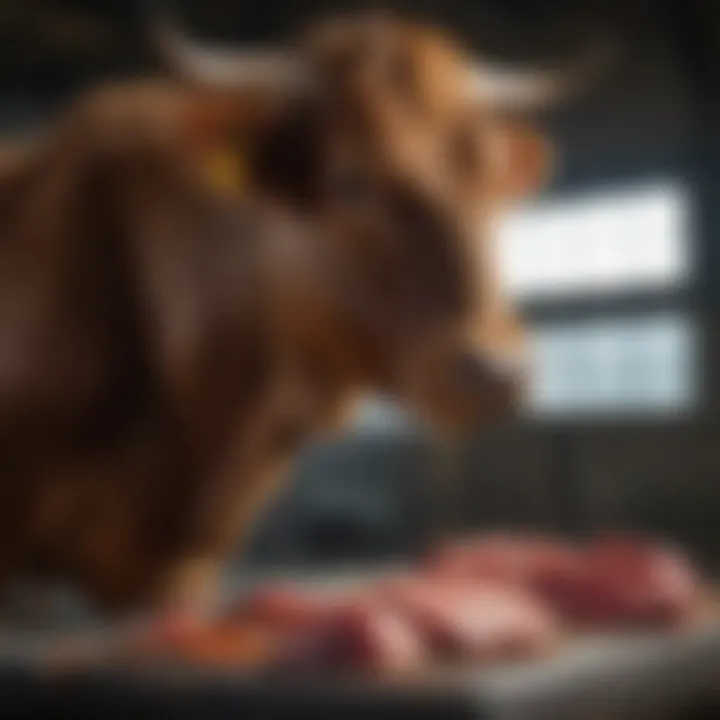
Manual skinning cradles are often favored by smaller operations or those who emphasize traditional methods. These cradles typically consist of a simple design, often made of durable metal or wood. A key characteristic of manual skinning cradles is their need for human intervention in the skinning process. Meat processors using these cradles do so with great skill and experience. Since manual cradles rely on human dexterity, they allow for a precise approach to skinning, which can be indispensable for certain cuts of meat that require special attention.
"The skill of the butcher can turn a potentially messy process into a work of art, preserving the quality of the meat while ensuring efficiency."
Among the benefits of manual cradles is the ability to control the skinning process closely. However, they can be physically taxing on workers, leading to fatigue over longer periods. Additionally, the final output heavily depends on the operator’s skill level. While manual cradles are often more economical upfront due to lower initial investment, their efficiency can be limited, especially in high-volume operations.
Mechanical Skinning Cradles
On the other hand, mechanical skinning cradles represent a leap into modern technology. These systems are engineered to automate much of the skinning process, thereby increasing both speed and efficiency. Mechanical cradles often utilize hydraulic or electrical systems to control the skinning task, which minimizes the physical demand on workers.
The technological advantages of mechanical skinning cradles include:
- Time efficiency: Speed up the skinning process, accommodating larger volumes of beef in lesser time.
- Consistency and quality: Maintain a uniform skinning technique, which can lead to improved meat quality across batches.
- Reduction of labor costs: By automating the process, fewer workers are required, allowing for labor resources to be utilized in other areas.
However, the investment for mechanical cradles is considerably higher, and they do require ongoing maintenance to ensure optimal functionality. An additional concern is that they may not be as adaptable to specific cuts of meat that require nuanced handling.
Advantages and Disadvantages of Each Type
When considering the types of skinning cradles, it’s clear that each has its own set of advantages and disadvantages that need careful thought:
Manual Skinning Cradles:
- Advantages:
- Disadvantages:
- Lower initial cost
- Greater operator skill involvement, leading to potentially higher-quality cuts
- Greater adaptability to unique cuts of meat
- Slower processing speed
- Physical strain on workers
- Greater dependence on individual skill level
Mechanical Skinning Cradles:
- Advantages:
- Disadvantages:
- Higher speed of operation
- Consistent output quality
- Less physical labor required
- Higher initial investment costs
- Regular maintenance required
- Potential lack of flexibility for certain specialized cuts
Understanding these aspects can significantly influence decision-making for meat processors. The choice between manual and mechanical cradles impacts not just the bottom line but also the quality and efficiency of beef processing as a whole.
Design Features of Skinning Cradles
Understanding the design features of skinning cradles is essential to grasp their role in beef processing. Each element in a cradle design serves a purpose, from material choice to ergonomic adjustments, all ensuring smoother operations and better meat handling.
Materials Used in Construction
The selection of materials in constructing skinning cradles is pivotal. Typically, these cradles are made with stainless steel or high-grade aluminum to resist corrosion and ensure cleanliness. Stainless steel provides robust durability, standing up to the harsh conditions of a processing facility. On the other hand, aluminum, while lighter, is often treated to enhance its resistance to wear and tear.
Matching the material to specific needs can prevent contamination. Non-porous surfaces are vital for maintaining hygiene, reducing the risk of bacteria growth. It’s not just about strength; the choice of material affects operational efficiency and the overall lifespan of the unit.
"The right materials can turn a functional instrument into a reliable partner in the meat industry’s daily grind."
Adjustability and Ergonomics
Having an adjustable design in skinning cradles isn’t just a luxury; it's an absolute necessity. Working with different sizes of carcasses demands flexibility. Cradles that can adjust height and angle give operators the ability to work more comfortably, reducing physical strain. This can improve speed and accuracy during skinning, which ultimately benefits the meat quality.
Ergonomic handles and supports play an important role too. If a cradle is designed with the end user in mind—meaning it accommodates natural body movements—it can dramatically decrease fatigue and enhance focus. An operator can navigate the skinning process more efficiently when their workstation fits comfortably around them.
Safety Features and Compliance Standards
In an industry where sharp instruments are commonplace, safety features are non-negotiable. Skinning cradles should include features like rounded edges to prevent accidental cuts, along with non-slip surfaces that ensure everything stays firm during operation. Safety harnesses for securing the carcass also reduce risk, preventing movement that could compromise both safety and efficiency.
Additionally, compliance with local safety standards is crucial. Regular inspections based on these regulations ensure that the equipment is up to par. This reduces liability and establishes a trustworthy environment for all personnel involved. Keeping up with compliance isn’t just good practice—it reflects a commitment to excellence in meat processing operations.
Operating Techniques for Effective Skinning
Operating techniques play a pivotal role in ensuring efficient and high-quality skinning of beef carcasses. The method employed directly affects not only the speed of the processing but also the overall quality of the meat. Efficient skinning techniques minimize the risk of damage to the carcass, significantly preserving the meat's integrity. A well-executed skinning process can lead to a more uniform product and reduce waste, which is a considerable advantage in a commercial setting.
Preparation of the Animal Carcass
Proper preparation of the carcass is crucial before the actual skinning begins. This stage includes various steps:
- Inspection: The carcass must be thoroughly inspected for any signs of disease or abnormalities that may affect the meat quality. If any concerns arise, proper protocols must be followed to prevent contamination.
- Hanging the Carcass: The animal's carcass should be hung in a way that allows easy access for skinning. Typically, a gambrel hook is used to suspend the carcass from its hind legs, facilitating the process.
- Cleaning the Area: Before starting the skinning, the work area around the carcass must be sanitized. Maintaining cleanliness reduces the risk of cross-contamination, ensuring that the meat remains safe for consumption.
- Tools Setting Up: Make sure that all necessary tools such as knives, hooks, and skinning cradles are ready. This minimizes downtime and ensures that the skinner can work swiftly.
Careful preparation sets the stage for a successful skinning process, impacting the quality of the end product.
Step-by-Step Skinning Procedures
Once the carcass is prepared, it’s time to move into the skinning procedures. Here’s an outline of effective steps:
- Initial Cut: Start by making a careful incision around the legs and brisket to loosen the skin. These initial cuts are critical as they guide the rest of the skinning.
- Skin Loosening: Use a knife with a sharp blade to carefully separate the skin from the underlying muscle. This takes patience and precise movements; rushing can lead to unwanted tears in both the skin and muscle.
- Progressing to the Midline: Continue loosening the skin around the midline towards the back of the carcass. Maintain uniform pressure to avoid cutting too deep.
- Final Separation: Once the skin is loosened sufficiently, grasp the skin and pull steadily, continuing to cut as needed. Working in a smooth, controlled manner is key to keeping the meat intact.
- Inspect as You Go: Continuously check for any unevenness or excess fat that may need trimming.
Utilizing these precise steps will help ensure that the skinning is efficient and reduces the likelihood of injuries or damage to the meat.
Best Practices for Maintaining Meat Integrity
To uphold the quality of the meat during and after the skinning process, consider the following best practices:
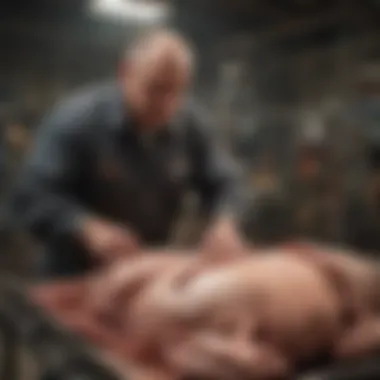
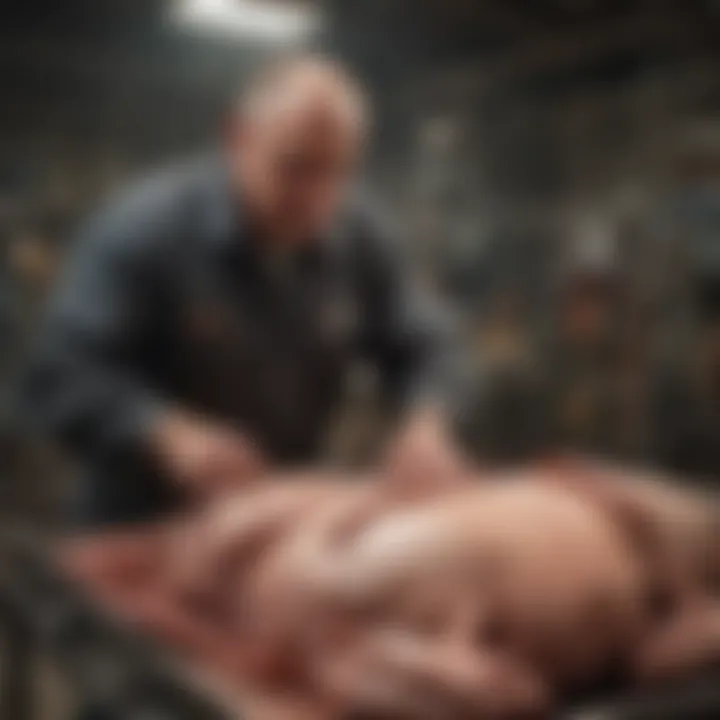
- Proper Knife Technique: A blunt knife can cause tears and damage; ensuring that knives are sharp and suitable for the task will protect the meat.
- Temperature Control: Ensure that the carcass is kept at optimal temperatures throughout processing to prevent spoilage. Proper refrigeration should be monitored carefully.
- Prompt Skinning: Although thoroughness is essential, it's also important to complete the skinning promptly to minimize exposure of the meat to harmful bacteria.
- Attention to Fat: Excessive handling of the fatty layers can lead to the release of enzymes that spoil the meat quality. Focus on making clean cuts that separate the skin without disturbing the fat excessively.
- Post-skinning Procedures: After skinning, ensure that the carcass undergoes proper butchering and further processing without delays. This adds another layer of quality control.
By diligently applying these best practices, processors can maintain the meat's integrity, optimizing both safety and quality, which are paramount in beef processing.
Always keep in mind that the quality of meat starts from the moment the animal is prepared for skinning. Each step in the process matters.
Impacts of Skinning Cradles on Meat Quality
The skinning cradle plays a pivotal role in the beef processing workflow, significantly impacting the overall quality of meat. A proper skinning cradle not only facilitates efficient operations but also preserves the meat's natural properties, ensuring higher standards of safety, taste, and texture. Understanding how skinning cradles affect meat quality is essential for professionals and enthusiasts alike in the agricultural sphere.
Preservation of Muscle Tissue
One of the most critical aspects of meat quality is the preservation of muscle tissue during the skinning process. When the hide is removed from the carcass, it’s vital to minimize damage to the muscle structure beneath. A well-designed skinning cradle stabilizes the carcass, allowing for a more controlled skinning process. This helps in maintaining cellular integrity, reducing the risk of bruising or tearing, which can negatively affect meat quality.
Moreover, when muscle fibers remain intact, they retain the moisture content better, contributing to juiciness and tenderness. If muscle tissue is disrupted, it can lead to a loss of fluids, ultimately drying out the meat. Thus, utilizing a skinning cradle that is both ergonomically designed and supports precise movements can yield better outcomes in meat preservation.
"The preservation of muscle tissue can often dictate the market value of beef products and consumer satisfaction."
Influence on Marbling and Fat Distribution
Marbling refers to the intramuscular fat within beef, which enhances flavor and tenderness. The way a carcass is handled during and after skinning can greatly influence how fats are distributed in the meat. Skinning cradles that allow for controlled handling can prevent excessive pressure on fat layers, leading to a more even distribution of marbling.
Proper handling also prevents the fat from being excessively rendered out, which can occur if the environment around the carcass is not properly controlled. A cradle that promotes a gentle and stable setup allows meat processors to achieve desirable fat characteristics more effectively.
In summary, by choosing the right skinning cradle and mastering the technique, professionals can promote optimal marbling, leading to superior flavor profiles and enhanced taste experiences for consumers.
Quality Control Measures in Skinning Processes
Implementing quality control measures during the skinning process is essential for ensuring the highest standards of meat quality. This includes proper training in using skinning cradles. Employees must be skilled in operating these tools correctly to avoid issues that could compromise meat quality.
Among the quality control practices to consider are:
- Regular Training Sessions: Keeping operators updated about the latest techniques.
- Routine Equipment Checks: Ensuring that skinning cradles are functioning as intended to prevent mechanical failures.
- Checklist Protocols: Establishing a step-by-step guide that workers can follow during skinning to minimize risks of poor meat quality.
Establishing these measures not only ensures consistency in the final product but supports the overall integrity of the meat processing operation. By placing emphasis on quality controls associated with skinning, the entire beef processing landscape can benefit significantly.
Maintenance and Care of Skinning Cradles
The effective use of skinning cradles directly hinges on regular maintenance and care. Grime and residue can accumulate quickly in these tools of the trade, potentially leading to operational difficulties or even unsafe handling practices. By implementing proper care routines, you not only extend the lifespan of the cradle but also ensure that meat quality is preserved during the processing phase. Let’s break down the various facets of maintaining these vital pieces of equipment.
Routine Cleaning Protocols
Cleaning a skinning cradle is not just about keeping it shiny; it’s an essential practice to maintain hygiene in beef processing. After each use, a thorough cleaning should be performed to remove any blood, hair, or other remnants left behind. Here’s a simple checklist for cleaning:
- First rinse the cradle with warm water to loosen residual dirt.
- Scrub all surfaces with a brush, preferably made from non-abrasive material, to avoid scratches.
- Utilize a food-safe disinfectant to kill any lingering bacteria; ensure it’s suitable for meat processing environments.
- Rinse thoroughly with clean water to eliminate any cleaning agents that could contaminate meat.
Implementing a cleaning schedule, possibly before and after shifts, can keep up these standards. Being consistent shows commitment to meat safety and quality.
Inspection and Troubleshooting
Regular inspections are a must to catch potential issues before they exacerbate. The importance of inspecting skinning cradles can’t be overstated, as small problems can turn into major complications.
When conducting an inspection, look for:
- Signs of wear and tear, such as cracks or rust on the metal parts.
- Any screws and bolts that are loose; tighten them as needed to ensure stability during use.
- Joints and hinges; these should move freely without excessive force.
If a malfunction is suspected, employ some troubleshooting tactics:
- Identify the unusual noise, smell, or behavior of the equipment. This often gives clues about what’s amiss.
- Replace parts where necessary. Having spare parts on hand can cut down downtime significantly.
Strategic Upkeep for Longevity
To maximize the lifespan of skinning cradles, a strategic approach is vital. Simple actions can yield tremendous benefits over time:
- Lubrication: Keep moving parts lubricated to prevent rust and ensure smooth operation.
- Storage: When not in use, cover the cradle to protect it from dust and airborne particles.
- Training: Educate staff on proper handling and care to mitigate avoidable damage. Maintaining a culture of responsibility around equipment care creates a conscientious workforce.
"Regular maintenance not only prolongs the life of equipment but also safeguards the quality and safety of meat products."
Safety Considerations in the Use of Skinning Cradles
The use of skinning cradles is a significant part of the beef processing operation. However, it's imperative to recognize that with these tools come certain safety risks. Ensuring safety in their application can help prevent accidents and injuries, promoting a better working environment for all involved in meat processing. The responsibilities surrounding the use of skinning cradles are crucial, and they can make all the difference in maintaining high operational standards and worker well-being.
Understanding Potential Risks
In the bustling world of meat processing, skinning cradles present specific hazards that workers may face daily. Among these risks are the potential for lacerations from sharp tools and equipment used during the skinning process. Here are some common points to consider:
- Sharp Instruments: Operators should be aware of the knife or blades being used while skinning. These can easily slip or cut if not handled correctly.
- Ergonomic Strain: Continuous lifting or maneuvering without proper body mechanics can lead to musculoskeletal injuries.
- Slips and Falls: Maintaining the area around the skinning cradle clear of debris is essential to help prevent accidents.
By identifying these risks, facilities can implement proactive measures to help mitigate them. Training staff to recognize hazards can create a safer working culture.
Personal Protective Equipment (PPE) Requirements
Another cornerstone of safety when working with skinning cradles involves the use of proper personal protective equipment (PPE). Employees should be outfitted with suitable gear designed to shield them from harm. Key components of an effective PPE strategy include:

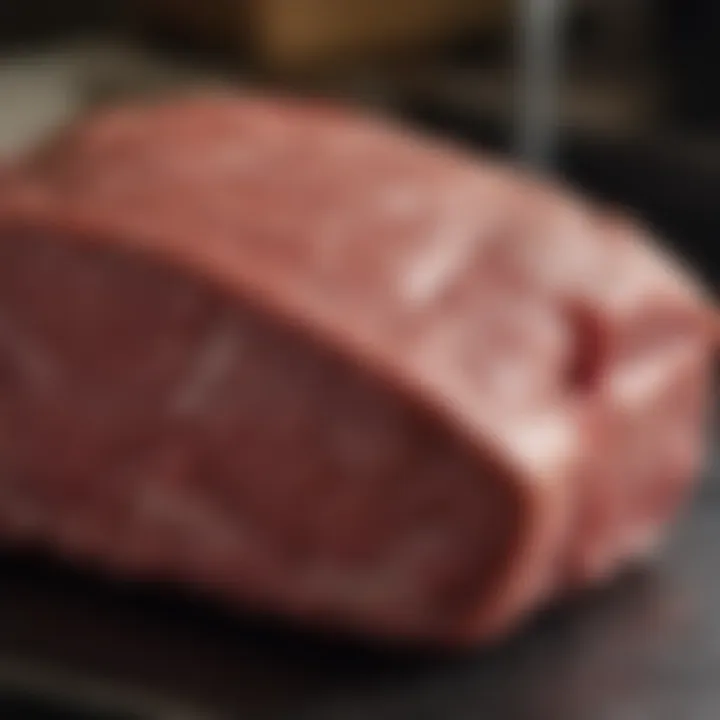
- Cut-Resistant Gloves: Using gloves specifically designed to resist cuts can help protect the hands when handling sharp tools.
- Aprons: Durable aprons can prevent cuts from errant knife movements and help reduce exposure to any cleaning agents used on the cradles.
- Safety Footwear: Steel toe boots can protect feet from heavy items dropping or rolling onto them during operations.
Investing in high-quality PPE is crucial for ensuring workers are safe while using skinning cradles. Regular training sessions on PPE adherence can also reinforce the habit of wearing protective gear.
Emergency Protocols and First Aid
Despite precautions, accidents can happen, and knowing how to respond in such situations is vital. Establishing effective emergency protocols can make a substantial difference in responding to incidents involving skinning cradles. Key aspects include:
- Accessibility of First-Aid Kits: Ensure that first-aid kits are easily available and stocked with necessary supplies, such as bandages, antiseptic, and gloves.
- Training on Emergency Responses: Regular training on how to handle emergencies helps reinforce appropriate behavior. Staff should know how to perform basic first aid and when to contact medical professionals.
- Clear Incident Reporting Procedures: Having a straightforward process for reporting accidents and injuries allows for proper documentation and systemic improvement in safety protocols.
"Safety procedures should never be seen as paperwork but rather as essential steps towards a safer workplace for everyone."
In summary, safety considerations in using skinning cradles are not to be taken lightly. A proactive approach that includes understanding potential risks, enforcing PPE requirements, and having robust emergency protocols can significantly enhance the safety and efficiency of any beef processing operation.
Technological Advancements in Skinning Cradles
Technological advancements play a pivotal role in modern skinning cradles, enhancing their effectiveness and utility in beef processing. As the meat industry evolves, incorporating cutting-edge tools and techniques becomes crucial for maintaining efficiency, safety, and product quality. When we look at the differences in older methods compared to the newest innovations, it becomes clear that technology does more than just streamline the process—it significantly impacts the overall end results in meat quality and processing speed.
Innovations in Design and Functionality
One of the most significant enhancements in skinning cradle technology is the design integration aimed at improving functionality. New materials like stainless steel boost durability and hygiene, address corrosion issues, and ensure a longer lifespan of the equipment. Additionally, cradles are now engineered with ergonomic considerations in mind, which means they can be adjusted quickly to fit the user’s height and body mechanics.
For instance, these cradles often include features like:
- Adjustable support angles that allow for optimal positioning of the carcass during skinning. This not only elevates the ease of skinning but also helps maintain meat quality by reducing undue strain on the muscle fibers.
- Enhanced grip surfaces that minimize slippage during the skinning process, improving both safety and efficiency.
The result is a more comfortable working environment, which can lead to increased productivity and reduced fatigue for the workers, ultimately benefiting the bottom line.
Integration with Automated Systems
In recent years, we’ve seen a noteworthy shift towards the automation of meat processing tasks, including skinning, through integrated systems. These sophisticated systems are designed not just to assist but to enhance the performance of skinning cradles.
Automation brings several benefits:
- Consistency and Accuracy: Mechanized systems can deliver uniform results every time, minimizing human error. This is incredibly important in maintaining meat quality and appearance.
- Increased Throughput: Automated skinning cradles can handle larger volumes at a faster pace than manual methods, which is a direct response to the growing demand for meat products.
- Data Tracking: Advanced systems can monitor performance metrics in real-time, allowing users to assess efficiency and make adjustments as necessary. This information is essential for continuous improvement.
The integration of these automated features into existing frameworks permits a smooth transition that can prepare operations for future demands without sacrificing current capabilities.
Future Trends in Meat Processing Equipment
Looking ahead, the future of skinning cradles in beef processing seems promising with continuous innovations on the horizon. Trends such as:
- Smart Technology: Think of cradles equipped with sensors that alert operators about maintenance needs or operational inefficiencies.
- Blockchain for Traceability: As consumers demand more transparency about their food sources, the incorporation of blockchain technology into skinning cradle operations can offer complete traceability of meat from farm to table.
- Sustainable Materials: There is a growing push towards utilizing eco-friendly materials in the manufacturing of equipment, responding to global sustainability efforts.
These advancements will not only drive improvements in efficiency and safety but will also align with consumer expectations for higher standards in meat processing.
"Innovation in meat processing is no longer just about speed—it's about quality, safety, and sustainability."
As we digest these developments, it’s vital for professionals in the meat industry to stay informed and embrace these changes. The goal is to not only improve operational capabilities but also to ensure that the end products meet the high standards that today’s consumers demand.
Investing in technologically advanced skinning cradles is not just an operational decision; it reflects a commitment to excellence in meat processing.
Case Studies: Successful Implementation of Skinning Cradles
Skinning cradles are not just tools; they represent a significant leap in the efficiency of beef processing operations. Understanding the real-world application of these cradles helps stakeholders grasp their impact not merely through technical specifications but through actual scenarios. Case studies illuminate how various operations have capitalized on the benefits these cradles offer, showcasing their pivotal role in enhancing both meat quality and operational efficiency.
Farm Operations Optimizing Meat Processing
Farm operations often lie at the heart of meat processing, where traditional practices meet modern innovations. One striking case comes from the Smith Family Ranch in Colorado. Here, the implementation of a state-of-the-art mechanical skinning cradle made a notable difference.
Prior to this upgrade, the ranch faced challenges with labor intensity and meat integrity during processing. Workers spent endless hours manually skinning, leading to inconsistent results and higher risk of injury. After integrating a mechanical skinning cradle, the efficiency of skinning tasks improved significantly. Not only did the time taken for skinning each carcass reduce, but it also minimized damage to the muscle tissue, which is crucial for meat quality.
This setup allowed them to process more animals in less time without sacrificing quality. Furthermore, it freed up the skilled workers to focus on other vital aspects of meat processing, leading to overall better product outcomes. The Smith Family Ranch’s experience illustrates how these cradles can act as a game changer, optimizing both time and labor in meat processing operations.
"Adopting technology isn’t just about keeping pace; it's about improving quality and efficiency simultaneously."
Efficiency Gains in Large-Scale Operations
In larger setups, efficiency translates directly to profit margins and sustainability. An excellent example here is the MegaMeat Processing Plant located in Texas, which processes thousands of cattle weekly. Their previous system relied heavily on outdated manual methods that burdened them with high operational costs and slow processing times.
When they invested in an advanced skinning cradle system, the results were remarkable. Implementation of this modern technology not only expedited the skinning process but also led to a reduction in waste. With greater accuracy in the skinning procedure, the plant saw a substantial increase in the yield of quality meat products.
In fact, reports indicated that meat output increased by about 20% within months of using the cradle. This improvement didn’t go unnoticed — the plant was able to enhance its competitive edge in a saturated market, drawing in more buyers eager for high-quality cuts. Also, higher efficiency in skinning meant less physical strain on workers, which bolstered workforce morale.
In the grand scheme of the meat industry, case studies such as those from the Smith Family Ranch and MegaMeat Processing Plant provide compelling evidence of the essential role that skinning cradles play. Their success narratives are not just isolated incidents; they underscore a broader trend in the beef processing landscape, where technology meets tradition to foster innovation and quality.
Finale
The conclusion of this article ties together the various aspects surrounding the use of skinning cradles in beef processing. This equipment is not just a tool but a central component that ensures quality, efficiency, and safety in the meat processing industry. Its design and operation play a significant role in preserving the integrity of the meat, preventing contamination, and maximizing yield.
Recap of Key Points
To summarize, several core points stand out:
- Importance of Design: The structure of skinning cradles impacts usability and functionality, optimizing the skinning process.
- Types of Cradles: Both manual and mechanical skinning cradles have their unique advantages, catering to different scales of operations.
- Techniques and Best Practices: Effective skinning techniques, preparation, and maintenance protocols directly influence meat quality.
- Safety Considerations: Understanding potential risks and adhering to safety standards are paramount for a smooth operation.
- Technology Integration: Innovations in skinning cradle designs are pivotal in modernizing meat processing for better productivity.
- Case Studies: Real-world examples highlight successful implementation, showcasing significant efficiency improvements in both large and small-scale operations.
Importance of Continuous Improvement
Continuous improvement in the handling and maintenance of skinning cradles cannot be overstated. As the meat industry evolves, so must the processes and equipment used. Adapting to new technologies and adhering to best practices ensures that the industry remains competitive and responsive to changing consumer demands.
Moreover, investing in training staff about the latest techniques and safety measures fosters a culture of excellence.