Comprehensive Guide to Air Compressor Houses
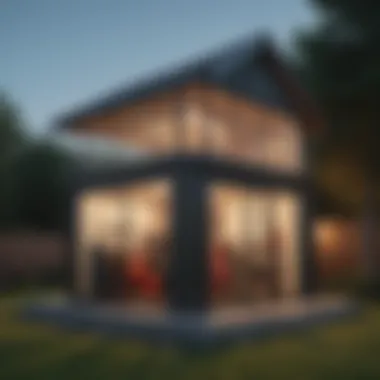
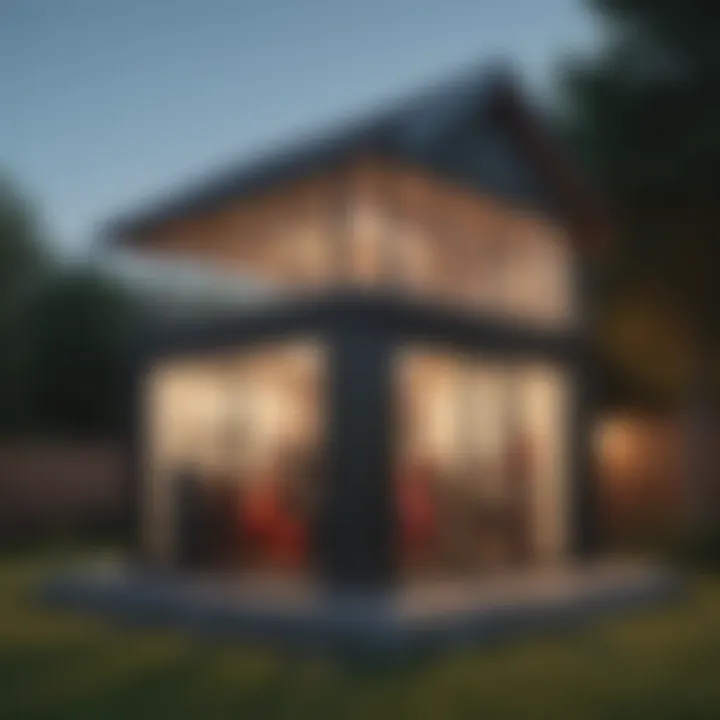
Intro
The construction and maintenance of air compressor houses are pivotal for optimal performance in various settings. Understanding the essential components and practices surrounding these structures is not merely a technical endeavor; it reflects broader trends in efficiency and sustainability, especially within agricultural and industrial contexts. This guide aims to shed light on best practices and innovations related to air compressor houses, emphasizing materials, design, and operational guidelines.
Current Trends in Agriculture and Horticulture
Overview of Recent Innovations
In recent years, the agriculture industry has seen significant shifts, focusing on efficiency and environmental friendliness. Innovations in air compressor technology are central to these advancements. Compressors are now designed with better energy efficiency, including variable speed drives and advanced control systems. This not only reduces operational costs but also contributes to lower carbon footprints.
Sustainable Practices Gaining Popularity
Sustainability is at the forefront of modern agricultural practices. There is a growing emphasis on integrating renewable energy sources, such as solar or wind power, into air compressor operations. This practice not only decreases reliance on fossil fuels but also lowers energy costs in the long run. Furthermore, many farmers are adopting practices such as rainwater harvesting to ensure that compressors operate efficiently during peak seasons.
Essential Farming Techniques
Soil Health Management
Soil health is critical for sustainable agriculture. Techniques such as crop rotation, cover cropping, and organic amendments play a significant role in maintaining soil integrity. These practices enhance nutrient availability while also improving water retention and reducing erosion.
Pest and Disease Control Strategies
Effective pest and disease management remains crucial. Integrated Pest Management (IPM) is a proactive approach that combines biological control, resistant varieties, and careful monitoring. Utilizing technology, such as drone surveillance, for early detection of pests can maximize yields while minimizing chemical inputs.
Tools and Technology in Farming
Overview of Advanced Farming Tools
Modern farming relies heavily on innovative tools and technologies. Precision agriculture is a prime example, encompassing GPS mapping and data analytics to guide decision-making. Farmers are also integrating air compressors for efficient operations in machinery, ensuring that equipment runs smoothly under various conditions.
Case Studies on the Use of Technology
There are numerous examples of how technology enhances agricultural efficiency. Farms utilizing state-of-the-art compressing systems report higher operational efficiencies and reduced downtime. Studies reveal a consistent correlation between advanced compressor systems and enhanced productivity across various farming sectors.
"The integration of advanced air compressor systems has revolutionized operational processes, driving efficiency in both agriculture and industry."
By understanding these trends and techniques related to air compressor houses, stakeholders can better position themselves within the evolving agricultural landscape. This guide underscores the importance of choosing the right materials, design, and operational protocols to ensure longevity and effectiveness of air compressors in diverse settings.
Prologue to Air Compressor Houses
Air compressor houses are essential structures in both agricultural and industrial settings. Their design and maintenance affect the performance of the air compressors housed within. Understanding the significance of air compressor houses is vital for anyone involved in these sectors. They serve as dedicated spaces to manage and safeguard air compressor systems, which in turn, influence overall productivity.
Oftentimes, the efficiency of agricultural operations hinges on the functionality of its equipment. Air compressors provide the necessary power for various agricultural tools and machinery, enabling activities like crop spraying, material handling, and livestock operations. Consequently, proper housing for these compressors ensures their longevity and reliable performance.
The Importance of Air Compressors in Agriculture
Air compressors in agriculture play a crucial role. They supply compressed air needed for pneumatic tools, irrigation systems, and crop treatments. As farms evolve towards automation and precision farming, the demand for reliable compressed air supplies increases. Efficient air compressors can lead to improved crop yields and better management of resources.
In addition to enhancing productivity, air compressors can optimize labor costs. By using pneumatic tools, farmers reduce manual labor while still achieving high standards for tasks such as planting and harvesting. The incorporation of air compressors means that farmers can accomplish necessary work faster and more efficiently.
A well-designed air compressor house contributes to the effective operation of these systems. It shields compressors from harsh weather conditions and provides an organized space for maintenance and repair. The strategic planning of air compressor houses leads to advantages in operational reliability and energy efficiency.
Defining the Air Compressor House
An air compressor house is essentially a facility designed to house air compressors and their related equipment. The design of this space should account for factors such as size, ventilation, and accessibility. These elements ensure that the housed equipment can function optimally without disruption.
An efficient air compressor house does not only protect its systems from environmental effects, but it also serves to enhance maintenance workflows. Proper layout and planning facilitate easy access for routine checks and repairs. This, in turn, prolongs the life of the compressors and minimizes downtime due to malfunctioning equipment.
It is also important to integrate safety features within the air compressor house. Proper design can prevent hazards related to fire, noise, and air quality. Overall, a thorough understanding of what defines an air compressor house is instrumental in achieving operational success in agriculture.
Design Considerations
Design considerations are crucial when constructing an air compressor house. This aspect involves numerous factors that significantly impact the operational efficiency and overall effectiveness of the air compressor system. A well-thought-out design not only accommodates the essential machinery but also ensures safe operation while optimizing airflow and user access. It is paramount to analyze the specific requirements of the air compressor to create a suitable environment that enhances durability and performance.
Size and Layout
Calculating Space Requirements
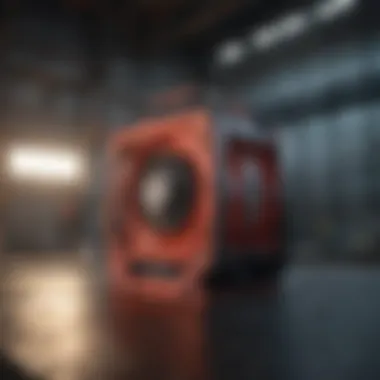
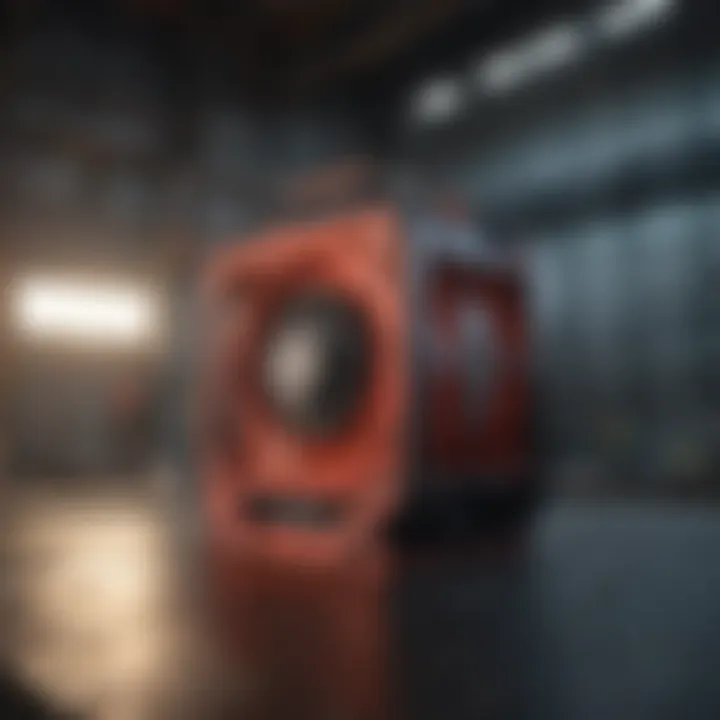
Calculating space requirements is a fundamental part of designing an air compressor house. It focuses on determining the total area needed to house the equipment efficiently while allowing room for maintenance and operation. The key characteristic of calculating space requirements is that it takes into account the physical dimensions of the air compressor and any associated machinery. For example, if a large rotary compressor is used, more space will be necessary to accommodate it and provide adequate airflow around it.
Understanding these space needs is beneficial because inadequate spacing can lead to overheating or operational interruptions. A unique feature of this process includes laying out the compressor locations to aid in airflow and accessibility. It is necessary to consider these elements because a poorly calculated space can lead to inefficiencies and higher maintenance costs.
Flow Patterns and Accessibility
Flow patterns and accessibility complement the overall operation of an air compressor house. This aspect emphasizes how air circulates within the space and how easily operators can access equipment for maintenance. A key characteristic of planning flow patterns is ensuring that air can move freely around all machinery. This prevents hot air from accumulating around the compressors, which could lead to malfunctions.
Accessibility is crucial for maintenance and safety. A well-planned layout means that operators can reach controls and perform repairs without significant delays. The unique feature here is the establishment of clear pathways for movement, thus promoting safety and efficiency. Its advantages include reduced downtime during maintenance, while the disadvantage could be an initial complexity in layout planning.
Structural Materials
Choosing Durable Materials
Choosing durable materials is an essential consideration in the construction of an air compressor house. Selecting appropriate materials involves understanding the long-term impacts on the structure's integrity. The key characteristic is their ability to withstand the condition of frequent usage and exposure to elements. For this reason, materials like steel or concrete are often favored.
Opting for durable materials ensures that the house lasts longer and requires less frequent repair, which can be a significant cost-saving benefit. However, the initial costs of these materials can be higher, but they often yield a better return on investment in the long run through longevity and reduced maintenance. This represents an essential balance to consider for stakeholders.
Insulation and Weatherproofing
Insulation and weatherproofing are vital parts of designing an effective air compressor house. Insulation minimizes energy loss and maintains consistent internal temperatures, which is crucial for compressor efficiency. One of the key characteristics of insulation is its effectiveness against temperature fluctuations. This can lead to increased energy efficiency, which is a clear benefit for agricultural operations that rely heavily on compressed air.
Weatherproofing protects the structure from rain, snow, and extreme temperatures, ensuring the air compressor operates smoothly regardless of outside conditions. The unique feature of this element is its role in preventing damage due to environmental exposure. The advantage of good insulation and weatherproofing lies in the reduced energy costs. However, inadequate insulation can result in increased energy waste and potential damage to machinery.
Essential Features of Air Compressor Houses
The design and construction of air compressor houses hinge on several essential features that ensure optimal operation. These features not only enhance the efficiency of the air compressors but also contribute to safety and comfort within the facility. Of particular importance are the ventilation systems and sound dampening techniques, which together create an environment conducive to effective machine operation while safeguarding the workersโ health.
Ventilation Systems
Types of Ventilation
Ventilation systems play a critical role in maintaining a stable atmosphere within an air compressor house. There are mainly two types of ventilation: natural and mechanical. Natural ventilation relies on airflow through openings, such as windows or vents, allowing fresh air to enter and stale air to exit. Mechanical ventilation, on the other hand, uses fans to control air movement in a more precise manner.
The unique feature of mechanical ventilation is its ability to provide controlled air exchange. This capability proves beneficial in environments where temperature and humidity levels fluctuates. Additionally, mechanical systems can filter out dust and contaminants, crucial for restoring optimal air quality. However, these systems can involve higher installation and energy costs compared to natural ventilation.
Maintaining Air Quality
Maintaining air quality is paramount in air compressor houses due to the potential build-up of harmful gases or vapors. Effective ventilation systems serve as the first line of defense. Regular monitoring of air quality helps identify issues that may arise over time.
The key characteristic of air quality maintenance systems is their capacity to detect and mitigate hazardous substances promptly. Proper maintenance of ventilation systems not only improves air quality but also increases the longevity of equipment. However, if not managed properly, these systems can become ineffective, leading to poor air quality and possible health risks.
Sound Dampening Techniques
Soundproofing Materials
Sound dampening is another essential feature of air compressor houses. High decibel levels can impact worker productivity and health. Therefore, implementing appropriate soundproofing materials is vital. Common materials include acoustic panels, sound barriers, and insulation layers that absorb and reduce noise levels.
These soundproofing materials are beneficial as they help create a quieter workplace, improving overall employee satisfaction and health. However, it is necessary to consider installation space and cost, which can vary significantly among different materials.
Optimal Placement of Machinery
The positioning of machinery significantly affects not only the efficiency of equipment but also noise levels. Optimal placement involves arranging compressors away from workstations and ensuring they are not directly adjacent to walls that may reflect sound.
One of the unique aspects of optimal placement is its contribution to airflow management and ease of access for maintenance. Proper planning in this area enhances operational efficiency by reducing potential downtime. Conversely, improper placement can lead to excessive noise and access difficulties, impacting maintenance schedules and overall efficiency.
"A well-designed air compressor house can significantly enhance performance and safety, benefiting all operations."
Safety Standards and Protocols
Safety standards and protocols are crucial in the context of air compressor houses. These guidelines establish a framework intended to minimize risks, ensuring the safety of personnel and equipment. When constructing and operating air compressor houses, adherence to safety protocols is not merely a best practice; it is an essential part of responsibility. Establishing these standards imbues a culture of safety that directly impacts productivity and operational efficiency.
Compliance with Regulations
Understanding Local Standards
Understanding local standards is vital in ensuring that air compressor houses meet the required safety expectations. Compliance with these standards can mitigate legal risks, ensuring operations do not face fines or shutdowns due to non-compliance. Each locality may have different regulations, driven by the types of industries present in that area, which can influence safety protocols. A key characteristic of understanding local standards is that it encourages alignment with community practices. This may also boost trust within the surrounding community, fostering better relationships with neighbors and stakeholders. However, neglecting local standards can lead to severe penalties and operational disruptions, which is why it is a beneficial choice for this article.
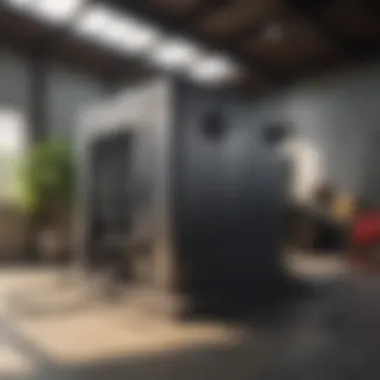
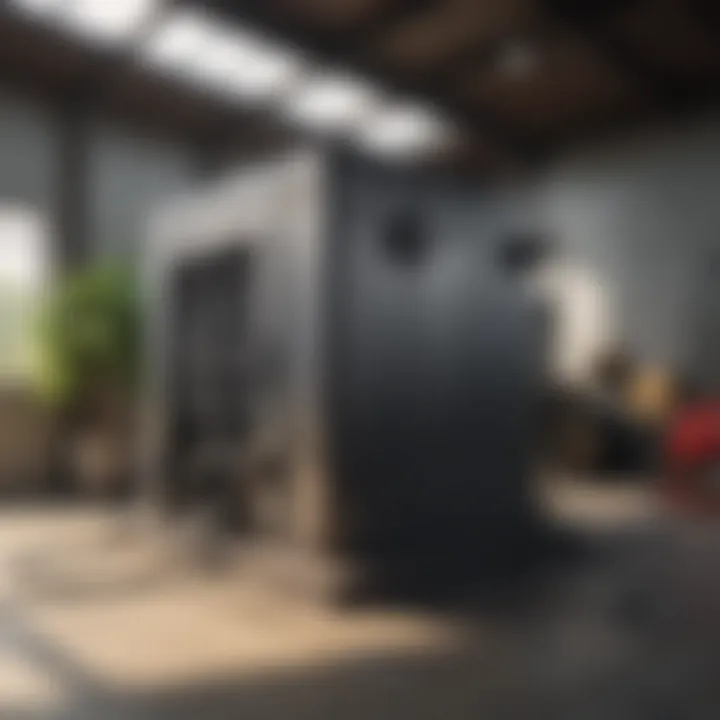
Documentation and Reporting
Documentation and reporting play an essential role in maintaining safety protocols. Accurate documentation helps track compliance with safety guidelines and can also help in future inspections. A key characteristic of effective documentation is that it provides a reliable source of information in case of incidents. Reporting mechanisms ensure that any safety breaches or maintenance issues are logged and addressed promptly. This aspect is beneficial as it enhances transparency and accountability within operations. However, the unique feature in documentation and reporting could lead to overwhelming amounts of paperwork if not managed well, which can distract from operational tasks.
Emergency Preparedness
Fire Safety Measures
Fire safety measures are one of the most critical components of emergency preparedness in air compressor houses. Given the nature of equipment used, the high-energy output can increase fire risks. Implementing rigorous fire safety measures helps in swiftly mitigating potential hazards. A vital characteristic of effective fire safety measures is the establishment of fire prevention protocols, such as routine equipment inspections and employee training. These measures not only secure the facility but also protect individual workers from potential harm. A notable advantage of comprehensive fire safety is that it can reduce insurance costs. On the downside, the initial cost of obtaining fire safety equipment and training programs can be substantial, although the long-term benefits often outweigh these costs.
Emergency Shutdown Procedures
Emergency shutdown procedures are essential in managing unexpected incidents safely. Having a clear and actionable shutdown plan can significantly reduce the risks during emergencies. The key characteristic of these procedures is that they can be tailored to the specific needs of the air compressor house, ensuring relevancy and effectiveness in various scenarios. Integrating structured shutdown protocols is beneficial as it protects personnel and frontline workers in critical situations. However, the unique challenge lies in ensuring that all operational staff are trained to execute these procedures effectively under pressure, which may require consistent training and reveiew.
Maintenance and Operational Guidelines
The efficiency and longevity of air compressor houses depend significantly on proper maintenance and operational practices. It is essential to perform regular maintenance to ensure that compressors operate at their optimal capacity. Neglecting these practices can lead to equipment failure, decreased performance, and increased operational costs. This section delves into the key elements of maintaining air compressor houses effectively, outlining routine tasks and troubleshooting common issues.
Routine Maintenance Tasks
Routine maintenance is crucial to keeping air compressor systems running smoothly. Regular checks and cleaning routines can prevent minor issues from escalating into significant problems that could result in unscheduled downtime.
Inspection Protocols
Inspection protocols form the backbone of a reliable maintenance plan. Regular inspections ensure that all components of the air compressor system are functioning as intended. A key characteristic of effective inspection protocols is their ability to identify early signs of wear or malfunction.
The benefit of such protocols is clear: they provide a framework for conducting systematic checks on equipment condition, vibration levels, and operational performance. Unique features, like the use of advanced minimal invasive diagnostic tools, allow for more frequent checking without significant disruption. However, the disadvantage may arise if inspection schedules are ignored, leading to potential equipment failures.
Cleaning Practices
Cleaning practices are another vital aspect of routine maintenance. Keeping the compressor and its components clean ensures that they perform efficiently. A primary characteristic of effective cleaning practices includes the removal of dirt and dust from components. This prevents overheating and efficiency loss.
The unique feature of a structured cleaning approach is its focus on preventative actions. For instance, maintaining cleanliness can extend the lifespan of filters and mechanical parts. However, if cleaning is performed too infrequently or improperly, it can lead to a buildup of debris, negatively impacting performance.
Troubleshooting Common Issues
Even with regular maintenance, problems may still arise. It is important to have guidelines for troubleshooting common issues that may occur in air compressor systems.
Identifying Performance Problems
Identifying performance problems is essential for maintaining operational efficiency. A pivotal characteristic of this process involves systematic monitoring of performance metrics, such as pressure levels and output rates. Detecting issues early can prevent further complications.
Having a method to consistently evaluate performance enables quick responses to abnormal findings. This proactive approach is beneficial because it can save time and resources. However, identifying performance problems may not always reveal the underlying issues, necessitating a deeper investigation.
Repair vs. Replacement Considerations
When issues are identified, decision-making between repair and replacement becomes crucial. Evaluating the extent of a malfunction against the age of the equipment is essential in this process. A key characteristic of this consideration involves assessing cost-effectiveness. Repair may appear cheaper short-term, but long-term replacements could be more fiscally sound.
Unique features of this consideration include the analysis of downtime, repair timeline, and parts availability. Assessing these factors holistically helps in making sound decisions. However, a disadvantage is that often, emotional attachment to older equipment may impede rational decisions about replacement.
Maintaining air compressor houses is not just about routine tasks; it's about creating an operational framework that emphasizes efficiency and long-term sustainability.
Efficiency in maintenance is not just about routine tasks. It's about creating an operational framework emphasizing efficiency and long-term sustainability. By understanding these guidelines and their interconnections, stakeholders can enhance overall productivity.
Technological Advances in Air Compressor Systems
Technological advancements play a crucial role in optimizing air compressor systems. As farming and industrial operations become more demanding, the need for efficiency and reliability increases. Therefore, integrating modern technologies helps to reduce downtime, enhance performance, and lower operational costs. This section discusses key innovations in air compressors that can greatly influence their effectiveness in both agriculture and industrial settings.
Integration with Smart Technologies
Remote Monitoring Solutions
Remote monitoring solutions are significant in modern air compressor systems. They allow operators to track performance metrics from off-site locations. The key characteristic of these systems is real-time data access, which provides insights into compressor efficiency, pressure levels, and maintenance needs. This capability enables timely interventions before minor issues escalate into critical failures.
One unique feature of remote monitoring solutions is their integration with mobile applications. Through such applications, users can receive alerts directly on their smartphones or tablets. This offers greater convenience and flexibility for operators. However, there can be challenges such as reliance on stable internet connectivity. Despite this disadvantage, the overall benefits greatly outweigh the risks.
Automated Control Systems
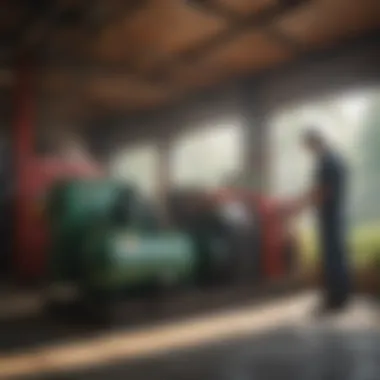
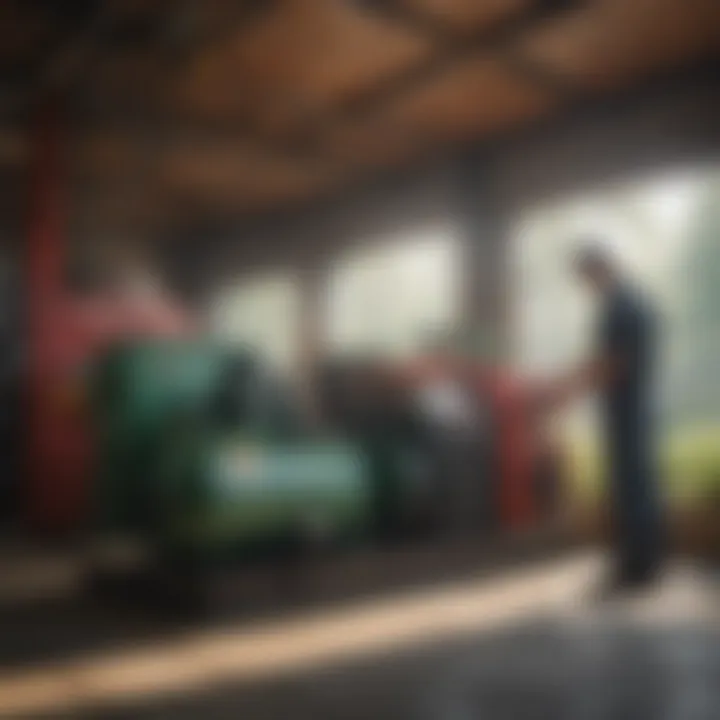
Automated control systems represent another leap forward in air compressor technology. These systems contribute by regulating operations according to real-time conditions and demands. A key characteristic is their ability to adjust operational parameters on the fly, ensuring optimal performance.
The unique feature of automated control systems is their self-regulating functionality. They can, for example, adjust the compressors' output based on fluctuations in demand. This results in significant energy savings and reduced wear on the equipment. On the downside, the initial investment can be higher compared to traditional systems. Yet, for many operators, the long-term savings justify the upfront costs due to increased efficiency and minimized downtime.
Energy Efficiency Enhancements
Energy efficiency enhancements are vital for modern air compressors. These advancements help in reducing energy consumption, which is essential for operational sustainability. Here, we shall examine two significant technologies: Variable Frequency Drives and Heat Recovery Options.
Variable Frequency Drives
Variable Frequency Drives (VFDs) are a cornerstone of energy efficiency in air compressors. They allow for precise control of motor speed based on actual demands, which minimizes energy waste. The key characteristic of VFDs is their ability to adapt to varying load conditions, leading to smoother operations.
A unique feature of VFDs is the reduced mechanical stress on the compressor components. This translates into extended equipment life and lower maintenance costs. However, they may require more complicated setup and monitoring to realize their full potential. Overall, the operational savings they provide often compensate for this complexity, making them a popular choice among users.
Heat Recovery Options
Heat recovery options are another powerful enhancement in energy efficiency. They enable the recovery and reuse of waste heat generated during compressor operation. This process can significantly improve overall system efficiency and reduce energy costs.
The key characteristic of heat recovery systems is their ability to convert wasted energy into usable heat for space heating or water heating. The unique benefit is that this adds an additional energy source to operations, often without requiring additional fuel. However, the effectiveness of the heat recovery system may vary based on the operating conditions and design of the compressor house. Nevertheless, investing in heat recovery options can lead to substantial long-term financial benefits.
Ultimately, adopting technological advances in air compressors can pave the way for enhanced productivity and energy efficiency in agricultural and industrial applications.
Economic Considerations
The section on economic considerations serves to outline the financial elements crucial for the design and sustained operation of air compressor houses. Understanding these aspects can greatly enhance the decision-making process for stakeholders, from farmers to industrial operators. Economic considerations encompass initial investments, setup costs, and ongoing operational efficiency, all vital for maximizing the economic viability of air compressor systems.
Initial Investment and Setup Costs
Budget Planning
Budget planning is a key factor in managing the initial investment and setup costs of an air compressor house. It involves a detailed assessment of all potential expenses, which range from construction costs to equipment purchasing. Having a robust budget plan helps in allocating resources efficiently.
A strong budget plan is beneficial because it allows stakeholders to anticipate costs and avoid overspending. Moreover, it aids in identifying areas where money can be saved without compromising quality. The main challenge is accurately predicting future costs. Market fluctuations can impact equipment and material prices, potentially leading to budget overruns. In this article, budget planning is positioned as an essential strategy for ensuring that the air compressor house facility is both effective and sustainable in the long term.
Financing Options
Financing options play an important role in managing the financial requirements of establishing an air compressor house. These options include loans, grants, or leasing arrangements that can reduce the upfront financial burden. Properly exploring financing opportunities can contribute to a more manageable investment landscape.
Key characteristics of financing options include flexibility in payment structures and the possibility of lower initial costs. Choosing the right financing arrangement can spread the cost over time, allowing for cash flow management. However, financing often comes with interest rates and other fees, making it necessary to conduct a thorough cost analysis to understand the total long-term implications. Thus, this section emphasizes the importance of evaluating different financing mechanisms to find the most beneficial paths for funding.
Long-Term Cost Efficiency
Operational Savings
Operational savings are crucial for the sustainability of an air compressor house. Effective management of operational costs can significantly impact the long-term financial health of an operation. Key areas for savings include energy consumption, maintenance frequency, and labor costs associated with running the air compressor systems.
One unique feature of focusing on operational savings is the ability to track and analyze energy usage over time. Implementing energy-efficient compressors and optimizing system performance can lead to substantial reductions in energy bills. While initial investments in more efficient technologies might be higher, the long-term savings often outweigh these costs, reinforcing the argument for energy conservation.
Return on Investment Analysis
Return on investment (ROI) analysis allows stakeholders to evaluate the financial returns generated by their investment in the air compressor house. Measuring ROI is essential for understanding the effectiveness of the investment against its costs. This analysis helps in determining whether the economic benefits justify the capital expenditures involved.
Key characteristics of ROI analysis include ease of calculation and clarity in revealing the profitability of an investment. A detailed ROI analysis can highlight the economic rationale behind choosing certain technologies over others, making it a popular choice for decision-makers. However, projecting ROI can sometimes be complicated by unpredictable variables such as market demand and operational changes. This section underscores the value of ROI analysis as a tool to assess the economic viability of investments in air compressor systems.
In summary, economic considerations in the context of air compressor houses are essential for understanding both initial setup and ongoing efficiency. By carefully planning budgets, exploring financing options, focusing on operational savings, and conducting ROI analyses, stakeholders can significantly improve their investment outcomes.
Epilogue
The conclusion of this article addresses how air compressor houses remain vital in optimizing agricultural operations. The proper design and maintenance of these structures directly influence the performance of air compressors, which are essential for various tasks in farming. High efficiency in compressor houses can lead to significant benefits in both productivity and sustainability.
Future of Air Compressor Houses in Agriculture
Air compressor houses are poised for transformation in the agricultural sector. The increasing reliance on automation in farming operations has heightened the demand for robust air compressor systems. As precision farming techniques become more prevalent, their integration with advanced air compressor technology makes it imperative to reevaluate designs and functionalities.
Farmers are likely to focus on energy-efficient compressors, which can drastically reduce operational costs. Pumps connected to renewable energy sources may enhance sustainability. Moreover, compact designs that facilitate easier placement and operation can emerge as popular solutions to accommodate modern agricultural spaces.
"Future advancements in air compressors will demand flexibility and adaptability in their housing to cope with evolving agricultural needs."
Final Thoughts on Optimization Strategies
In summary, optimizing air compressor houses involves a multi-faceted approach. Enhancing energy efficiency, reducing noise pollution, and ensuring effective maintenance are critical components. Farmers and operators should consider energy-saving products, such as variable frequency drives, to increase efficiency. Regular maintenance schedules play an essential role in extending the lifespan of compressors and adapting to advancing technology.
Implementing smart technologies for monitoring and controlling air compressor systems can lead to significant gains in operational efficiency. These strategies ensure that air compressor houses continue to serve as indispensable assets in agriculture, promoting better performance and sustainability.